- Magazine
- Material science insights
- What are the different rubber molding processes?
What are the different rubber molding processes?
What are the main molding methods for processing silicone rubber?
Silicone rubber molding processes vary as a function of the characteristics of the final product to be produced and a very large series of criteria, including (but not limited to) the manufacturer’s industrial facilities, batch sizes, economic considerations, regulatory constraints, etc.
To facilitate these various processing methods, the silicone rubber supplier must work closely with manufacturers to provide them with right formulations for their processes. To do this, silicone suppliers use the versatile chemical structure of silicone, based on alternating units of silicon and oxygen to design and produce their formulations. These are further enhanced by the integration of additives into the molecular framework. The result is that silicone formulations are available for manufacturers with an almost limitless series of characteristics, delivered in a wide range of formats, adapted to optimize different processes.
What is LSR (Liquid Silicone Rubber) injection molding and how does the process work?
LSR (Liquid Silicone Rubber) is specially formulated for producing technical parts, where strength, resistance and high quality are a must. Its main processing feature is that it is “flowable” or “liquid”, using unheated liquid or viscous material that is pumped by an injection nozzle into the mold cavity and is then easily funneled into a pre-heated cavity and vulcanized using additive curing with platinum. This simplifies and speeds up the manufacturing cycle and makes it ideal for economical production of high-volume parts.
The main stages in LSR injection molding processing are the following:
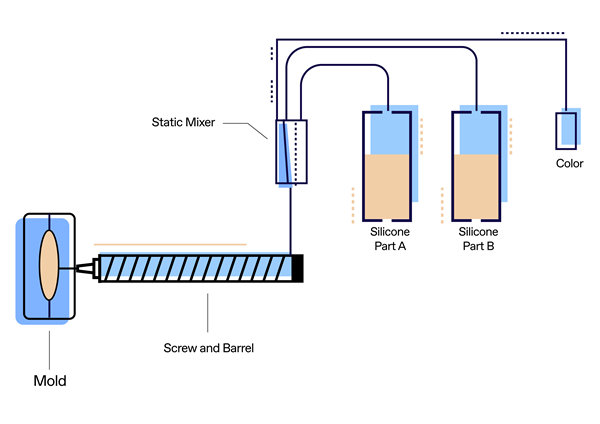
- The two-component platinum-cured silicone (as well as coloring) ingredients are directly introduced in different proportions via three hoses from pails or drums (varying in volume from 20 to 200 liters) into a static mixing unit and then pumped into the mold via a screw enclosed in a barrel.
- If we look more closely at the stage inside the barrel, once the LSR has been mixed and colored (if required), the silicone rubber is forced into the preheated mold (approximately 130° to 200°C) through a nozzle, with enough pressure to fully fill the mold cavity. Once this is finalized, a valve shuts off the flow and the next batch of LSR enters the barrel.
What are the differences between LSR and thermoplastic injection processing?
To begin with, machines for both types of material are very similar, with the same mechanical parts for moving the materials and the actual mold itself. The only notable difference is that thermoplastics are heated to remain viscous and that the pressure required to move the material is several thousand times higher for thermoplastics than for LSR (operating under 1000 PSI). While tooling parts for LSR are generally less costly than for thermoplastics, this may vary as a function of the dimensions and complexity of the final product. Some machines can handle both types of material and, in some cases, LSR and thermoplastics can be over-molded for certain applications. After the silicone or thermoplastic have cured and the mold has cooled, the parts are removed. Cycle times for both materials are about the same.
What is HCR (High Consistency Rubber) injection silicone molding and how does the process work?
HCR injection silicone molding, also referred to as Heat Cured Rubber or HTV (High Temperature Vulcanizing), uses reactive silicones with very high-weight macromolecules.
Various raw materials, such as fumed or precipitated silicas can provide customized features to HCR, such as high specific surface areas to improve mechanical properties, heat stabilizers, plasticizers or anti-structuring agents. Manufacturers need to find a balance between the advantages and disadvantages of HCR in injection molding. On the plus side, HCR raw materials and processing equipment are less costly, but on the other downside, HCR injection processing is less productive and requires more labor. This tradeoff must be carefully analyzed and implemented, depending on batch size and the final rubber product to be made, which is usually best done when manufacturers work closely with their silicone suppliers.
HCR raw materials come in single pre-mixed cured compound. They provide outstanding properties such as exceptional mechanical strength in a wide range of temperatures (-50°C to +300°C), very high resistance to aging and high-performance insulation. They can also be enriched with additives and fillers for critical applications in all industries, such as gaskets in combustion engines.
The main stages in HCR injection molding processing are the following:
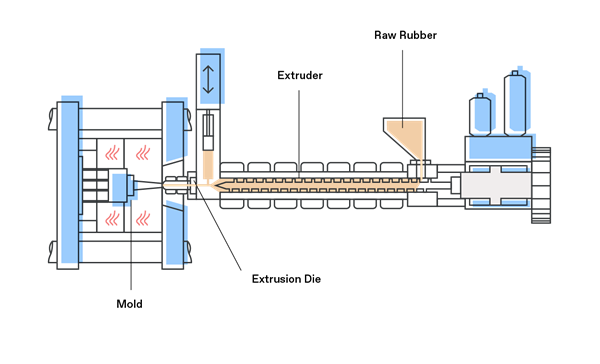
- A measured amount of HCR material is released into the injection molding machine. It is then injected directly from a cylinder through a screw mechanism and a nozzle into a closed heated mold, through a gate. The material fills and packs the cavities of the mold to form the part.
- HCR is vulcanized in the mold at higher temperatures than LSR, generally using peroxide for curing. It is then cooled to enable demolding, which is carried out manually by operators or automatically. Operators then proceed to trimming or other steps to compensate for some unwanted shape distortions caused by the demolding. They must also deal with deposits of acid powders, known as “blooming”, which require post-curing in a separate oven.
What is silicone compression molding and how does the process work?
Silicone compression molding is a time-tested processing method where a pre-vulcanized silicone raw material is simply placed between a two-part heated mold that is then sealed with a clasping system and compressed to fill the entire cavity. Depending on the part to be made, it usually uses HCR, but can in some cases use LSR or RTV materials. To finalize the process and produce the part, the heat and pressure are maintained until the silicone has cured.
The main stages of compression molding processing are the following:
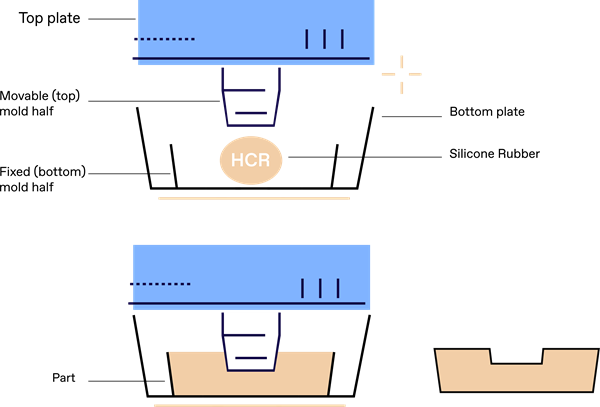
- A precise amount of the silicone raw material, pre-vulcanized into a doughy texture and pre-colored (if necessary), is inserted into half of the die cavity and then clasped shut with the other half of the mold. The two plates are then placed in a compression press and clamped at pre-determined pressure and temperature levels so that the silicone rubber entirely fills the cavities and begins to cure.
- Pressure is then released and the compression mold is removed and opened manually. The operator then inspects the part and proceeds to trim or finish it, sometimes by deflashing.
Compression molding is very efficient for simple or basic designs, whereas injection molding is more adapted to complex parts or rubber products. Compression molding is also well adapted for making larger parts that cannot be produced using extrusion techniques and is mainly used for low and medium batch volumes.
What is silicone transfer molding and how does the process work?
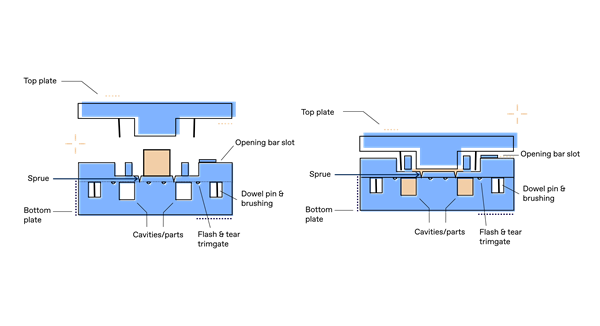
Transfer molding is in many ways like compression molding: generally using HCRs and pressure in an auxiliary chamber (known as a transfer pot) in a closed mold system. It differs from compression in that the mold is fully enclosed and not in two parts. It also differs from injection molding in that it requires higher pressure to fill the mold. Its main advantage is that it can integrate added fibers (including glass, carbon, aramid, natural plant fibers, etc.) on its outer layers and can also be ‘overmolded’ to produce customized high-strength -parts.
Transfer molding is therefore excellent for making high-precision geometrically complex parts in a short production cycle, with competitively priced tooling parts.
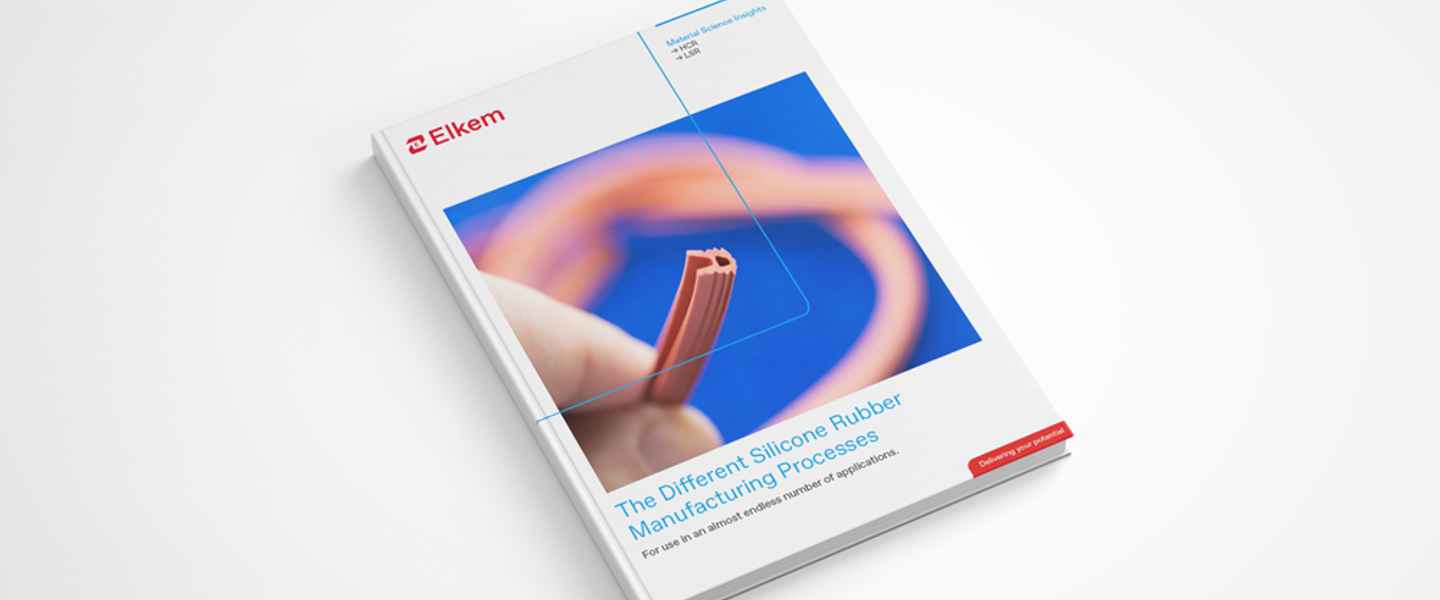
EBOOK - The Different Silicone Rubber Manufacturing Processes
For use in an almost endless number of different applications.