- Material Science Insights
- What are the different processing methods for silicone rubber?
What are the different processing methods for silicone rubber?
What are the processes for silicone transformation?
Silicone processing methods are a series of widely used manufacturing processes which transform silicone rubbers to create a final product with specific characteristics: shape, hardness or elasticity, color, degree of transparency, tear strength, resistance to environmental or mechanical stress, etc.
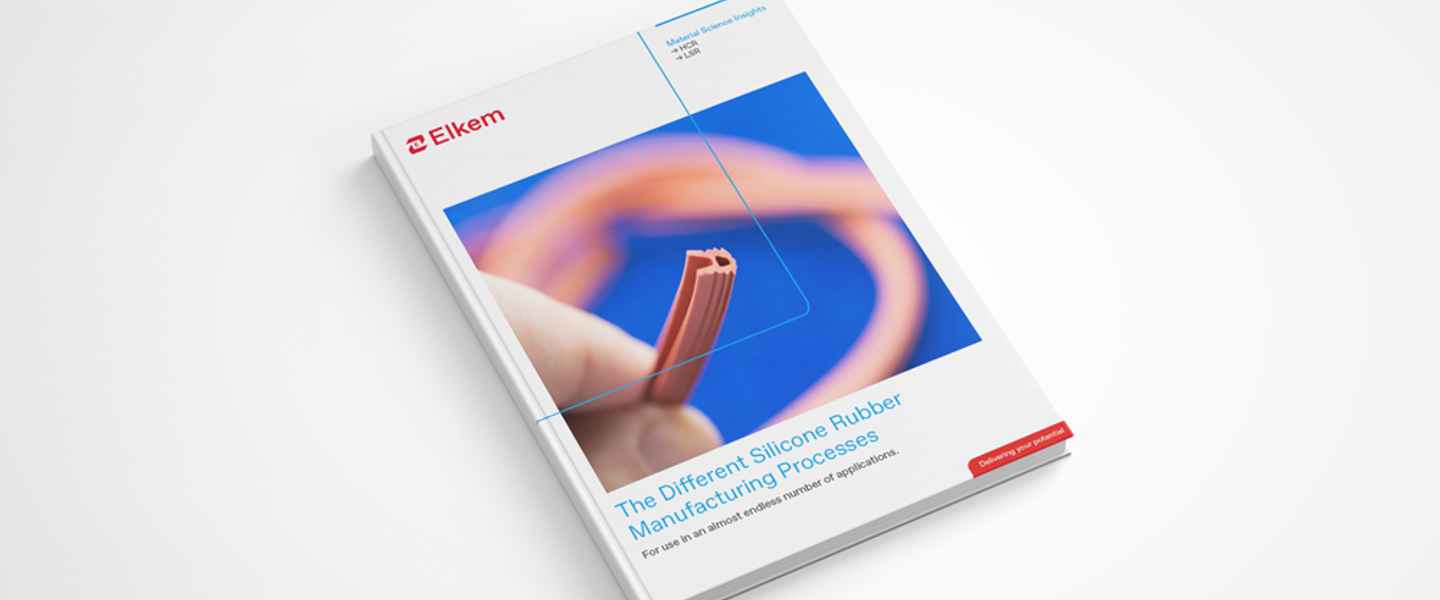
EBOOK - The Different Silicone Rubber Manufacturing Processes
For use in an almost endless number of different applications.
The reason why silicone rubbers are so versatile is because they have a chemical structure based on alternating units of silicon and oxygen. They can be manufactured with different organic and carbon groups, as well as additives and fillers that are integrated into their molecular framework. According to the combination of organic groups and the compounding methods used, silicone rubbers are available in a wide range of formats, enabling them to be adapted to different manufacturing processes for the making an almost endless number of products.
The most widely used processes are:
- Injection molding for High Consistency Rubber and Liquid Silicone Rubber
- Compression Molding
- Transfer Molding
- Extrusion
- Calendering
The choice for using one or another of these processing techniques depends on several factors: the complexity of the component, its size, the number of units produced, available budgets, the need for special characteristics, durability, etc. Therefore, it is essential to understand the materials and processes to optimize quality, productivity and consistency. Let’s have a closer look at these techniques.
Liquid Silicone Rubber (LSR) injection molding
Liquid silicone rubber is a high-purity, two-component platinum-cured silicone reinforced with specially treated silica. It is specially formulated for producing technical parts, where strength, resistance and high quality are a must. LSRs are less viscous than HCRs and therefore pumpable materials, ideal for liquid injection molding.
The primary difference between LSR and HCR is the “flowable” or “liquid” nature of LSR materials. Also, while HCR can use either a peroxide or a platinum curing process, LSR uses only additive curing with platinum. Due to the thermosetting nature of the material, LSR injection molding requires special treatment, such as intensive distributive mixing, while maintaining the material at a low temperature before it is pushed into the heated cavity and vulcanized.
How does the LSR injection molding process work and what advantages does it produce?
LSR injection, like its HCR counterpart, is used for creating molded end-products in cavities. The LSR process uses unheated liquid or viscous material that is pumped by an injection nozzle into the mold cavity. The raw material is simply funneled into the closed heated cavity using pressure, instantly filling the cavity. Because of its simplicity, LSR injection molding is a very rapid manufacturing method, extracted directly from drums or pails using a dosing unit, with fast turn-around time, ideal for producing very high volumes of parts
The main advantages of LSR injection molding include:
- Short and accurate molding cycles
- High volume production
- Efficient and economical processing
- Versatility for making a wide range of general-purpose products
- Fast curing and excellent mold release
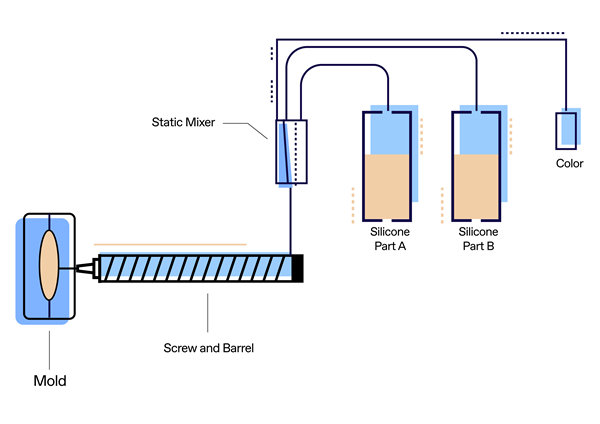
High Consistency Rubber (HCR) injection molding
High Consistency Rubber (HCR) is also referred to as Heat Cured Rubber or HTV (High Temperature Vulcanizing) silicone rubber. This material is made from reactive silicone with very high-weight macromolecules.
Various raw materials can provide specific features to the HCR, such as fumed or precipitated silicas with high specific surface areas to improve mechanical properties, heat stabilizers, plasticizers or anti-structuring agents.
HCR elastomers are superior to conventional organic elastomers, providing exceptional mechanical strength at temperatures ranging from -50°C to +300°C. They also age well, are chemically inert, stable when exposed to light or oxygen and can be colored easily or even be transparent, ideal for food packaging and paramedical applications. Addition of various additives to HCR opens unlimited customization solutions for existing and new applications in a wide range of industries: Aerospace, Automotive, Healthcare, Oil & Gas, Construction, Electronics, EVs, etc.
How does the HCR injection molding process work and what advantages does it produce?
A measured amount of HCR is injected directly from a cylinder through a screw mechanism and a nozzle into a closed heated mold, through a gate. The material fills and packs the cavities of the mold to form the part.
The main advantages of HCR injection molding include:
- Short and accurate molding cycles
- Lower unit costs
- Low waste of material
- Possibility of mixed molding with other materials, such as plastics or metals
- Consistent production, in terms of finished products
- Superior precision and filling for complex parts compared to, compression or transfer molding.
It is arguably the most common and robust molding method, in which the product can vary greatly in size, complexity, and application.
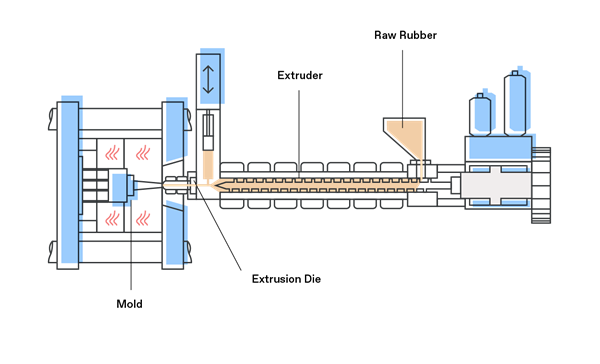
Silicone rubber extrusion
Silicone rubber extrusion is generally used to make hoses, cords, complex profiles and cross-sectional parts, usually quite long and often multi-layered components, as well as rods, oven seals, electrical cables, wire insulation, gaskets, seals, etc. The process uses an HCR compound with catalysts that is preformed into a strip or loaf. The preform is then fed into a screw extruder that forces the compound through a hardened steel die with a cutout pattern. The profiled silicone then passes through a heated compartment on a conveyor and is cured by continuously pulling it through an oven.
The main challenge for manufacturers using this technique is to choose the right grade of silicone rubber with the adapted catalyst system that will perform best in their specific mechanical and temperature and speed-controlled processes and will enable the final products to meet specifications, tolerance criteria and comply with regulatory standards.

Silicone rubber calendering
Calendering is a mechanical process that involves compressing and smoothing a material in a continuous manner by moving a sheet through pairs of heated rolls. These double or multiple hard steel roll sets are known as calenders. They are adjusted for pressure to produce a predetermined and uniform thickness, surface finish and texture for silicone rubber which can be shiny, matte, smooth, adherent or embossed, etc.
The raw material, typically HCR, which determines the mechanical properties of the finished product, is previously heat softened or extruded and then forced through the aligned cylindrical rolls. The calendering process presses the uncured silicone preform into a continuous silicone sheet. The silicone can then be pressed onto various substrates such as release film liners or combined with a variety of fabrics, glass, plastics, etc.
The main advantages of calendering processing include:
- High-volume, continuous processing of quality products
- Standalone sheets (unsupported) delivered in protective liners or products in combination with other materials, including organic or artificial fabrics (polyamide, viscose, polyesters, etc.), glass, plastics, etc.
- Almost endless applications, from liners for construction, home products, clothing, upholstery, food contact products, industrial conveyor belts, autoclavable products for medical applications etc
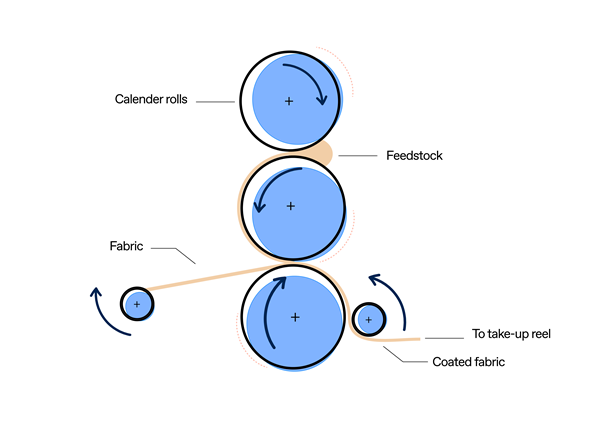
Silicone rubber compression molding
For this process, the silicone rubber remains flexible and then placed in a heated mold and closed using a sealed clasping system, with pressure applied to force the material to fill the entire cavity. The heat and pressure are maintained until the silicone has cured.
Compression and injection molding are similar in that they fill a preformed cavity, but they are different in that compression molds are prefilled directly with the charge, while in injection molding, the charge is injected into a previously fully closed cavity.
Manufacturers of different types of parts often use both compression and injection molding but for different types of parts. Generally, injection molding is preferred for making more complex (and often smaller) parts, while compression is very efficient for simple or basic designs and large parts that cannot be produced using extrusion techniques.
Other points of comparison include the fact that Injection molding has a shorter cycle time and so is often faster and more cost-effective for large volumes, while compression molding is mainly used for low and medium production series of parts.
The main advantages of compression molding processing include:
- Lower tooling costs
- Very little waste of material providing
- Cost effective, especially for large parts, but sometimes requiring post-mold finishing processing due to unequal product consistency and some flashing (gaps not always fully hollowed in grid patterns)
- Useful for some very large parts that cannot be made with extrusion molding
- Excellent for curved parts and useful for designing aesthetically creative parts, widely used in the automotive industry, often replacing metal parts to lower weight and save energy
- Used in several industries, including keypads for computers, kitchenware, electrical parts and some medical and dental devices.
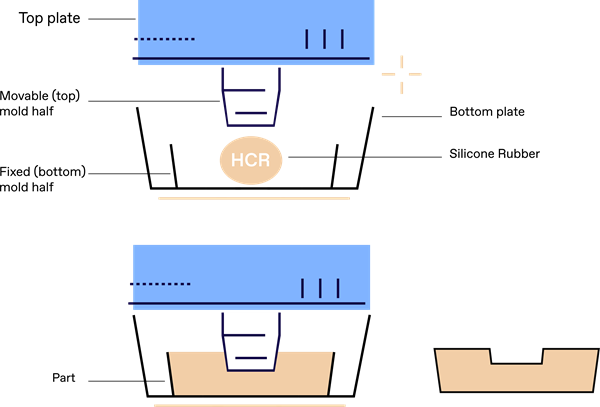
Silicone rubber transfer molding
Transfer molding is similar to compression molding in several ways: it uses HCRs, pressed from an auxiliary chamber (known as a transfer pot) into a closed pressurized mold system that incorporates a heated container above the mold where the silicone rubber is charged using a piston-powered gate and runner system that can move relatively hard materials into the mold before heating.
The silicone rubber transfer molding process is ideal for manufacturing high precision silicone molded parts as well as ‘overmolding’ with other materials, thus enabling the molding of complex geometries. The combination of HCR and the transfer molding process leads to high quality manufactured parts that offer design flexibility and shorter production cycles.
Transfer molding differs from compression in that the mold is fully enclosed and not in two parts. For this reason, it also differs from injection molding in that requires higher pressure to fill the mold. This also allows transfer molding to accept added fibers or matrices on its outer layers, to produce customized reinforced parts.
The main advantages of transfer molding processing include:
- Reduced tooling costs
- Uniform, accurate and more consistent parts compared to compression molding due to the one-piece mold and high dimensional tolerance
- Efficient and agile capacity for accepting different reinforcement fibers pre-positioned in the mold, including glass, carbon and aramid, as well as natural plant fibers.
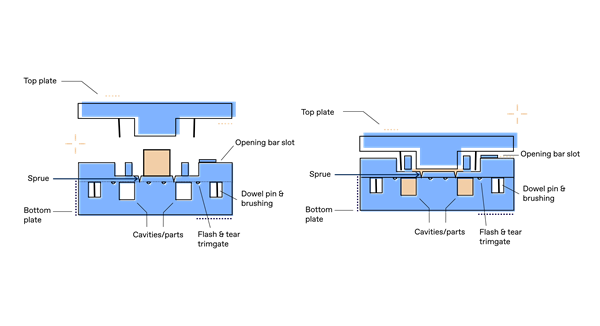