- Magazine
- Trainee Blog
- Elkem technical trainee programme: From "krampestudent " to industry apprentice
Elkem technical trainee programme: From "krampestudent" to industry apprentice
From student life to the professional world, Annlinn's journey as a technical trainee at Elkem has provided a supportive, educational introduction to working in the industry. She shares her experiences from the first day at the Thamshavn plant, working with Elkem MICROSILICA® and undergoing Elkem's supportive onboarding process for its technical trainee programme.
I recently transitioned from being a student to stepping into the professional world as a technical trainee and industry newbie. Before joining Elkem’s technical trainee programme, my work experiences were entirely in scientific research and laboratory work, so you can imagine the mix of excitement and awe I felt walking through the gates of the Thamshavn plant for my first rotation. Currently, I’m part of the PRIMA (Product, Innovation, and Market) group at Elkem Thamshavn, where I focus on the densification of Elkem MICROSILICA®—a topic we’ll dive into shortly.
Settling in, onboarding and first impressions
Stepping into a full-time job straight from a university classroom can feel overwhelming, and as many trainees share on this blog, it’s a phase filled with new locations, routines, connections and experiences. However, I took a slightly different approach by choosing to remain in Trondheim, the city where I spent my student years and now enjoy life as a so-called krampestudent. There’s no perfect English translation for this, but it is perhaps best described as someone reluctant to leave the student life behind.
This decision has made the transition smoother, but there is no need to worry if your old network is in a different location to your new job or rotation—at Elkem, there’s no shortage of fun outside the office. My journey at Thamshavn kicked off with a blåtur (a surprise outing) to Frøya, featuring team building, a RIB tour and good food—an easy way to connect with new colleagues. Other out-of-office activities include running the team marathon relay at Trondheim Marathon, regular lønningspils (payday beers) and weekly climbing sessions.
One of the highlights of my first months at Elkem has been the thoughtful and well-organised onboarding experience. It commenced with a smaller onboarding programme in Kristiansand, where first-year Norwegian trainees, along with trainees based in Kristiansand, had the chance to get to know each other and dive into an introduction to Elkem and the key tools utilised in the organisation. A few weeks later, the “official” onboarding in Lyon brought together trainees from Norway, France, and China for a global gathering, which was a great chance for intercultural exchange of trainee experiences and to learn about the endless possibilities for future outplacements.
Having spent my first few weeks at Thamshavn shadowing operators in the smelting plant, it was intriguing to explore how the silicon produced there connects to downstream processing and applications, such as those at Elkem Silicones in Lyon. It’s fascinating to see the journey from quartz to silicon to silicone—who knew a hard stone could become so soft and versatile? And, of course, we couldn't visit Lyon without a walk in the old town and indulging in the French cuisine—we happily ate our way through the city. A great appreciation to everyone for the warm hospitality and excellent organisation.
![]() Tour of the laboratory at ATRiON: the new Research and Innovation centre of Elkem Silicones
|
![]() Group photo from the Lyon trainee gathering and onboarding
|
![]() One of many great introductory presentations held at ATRiON
|
![]() Tour of the Roussillon site: an upstream site where silicon metal is converted into chlorosilanes, vinyl chlorosilanes and siloxanes
|
Diving into Elkem MICROSILICA®: My key focus this rotation
Now onto what I actually do.
I work with Elkem MICROSILICA®, a co-product of silicon or ferrosilicon production, made up of ultrafine (sub-micron), amorphous, non-porous, and perfectly spherical silicon dioxide (SiO2) particles. MICROSILICA® enhances the performance of concrete and cementitious systems by improving particle packing and initiating a pozzolanic reaction with calcium hydroxide, boosting strength and durability. The structure and large surface area of MICROSILICA® also make it valuable for refractory materials, enhancing sintering and high-temperature performance.
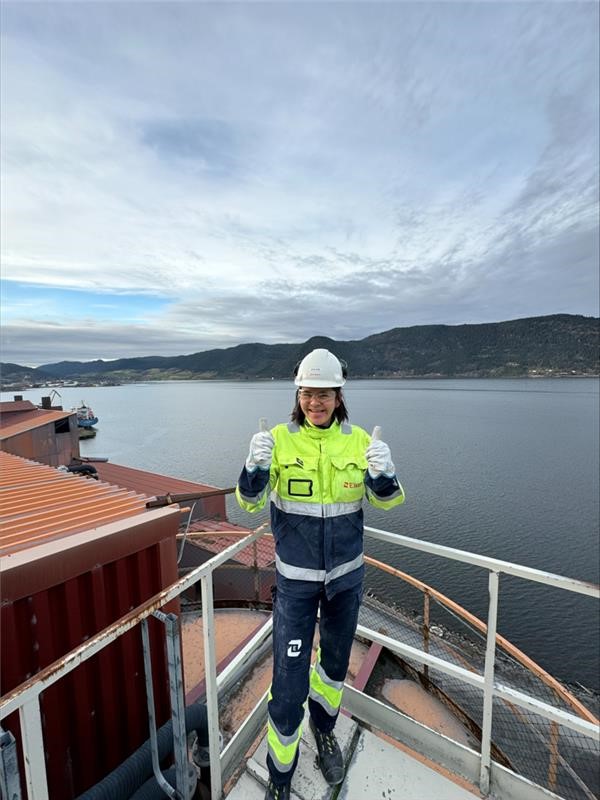
After MICROSILICA® leaves the furnace, it undergoes densification to improve handling, storage, and performance. While the densification process may seem straightforward, it’s influenced by variable furnace outputs, many external and process parameters, presenting both challenges and opportunities for further optimisation. This is where I come in.
My main objective is to analyse and optimise some densification process parameters, and to gain a deeper understanding of how different factors affect MICROSILICA® properties. To achieve this, my goal has been divided into smaller, more manageable tasks. It consists of a good mixture of sample collection, lab tests, data analysis, collaboration with various teams, as well as installing and configuring a new lab instrument. It has also included a trip to Elkem Fiskaa in Kristiansand for a densification workshop, which, much like my trainee period so far, provided a great opportunity to learn from some highly knowledgeable and experienced individuals.
This final point is a great way to sum up my first three months as a trainee at Elkem—the experience has given me insight into the industry and the chance to learn, not only about my focus area, MICROSILICA®, but the whole production process from smelting furnace, to MICROSILICA®, supply chain, laboratory and quality control.
As a trainee, you’re supported by a network of people eager to involve you in exciting tasks and guide you to success, all while accommodating your learning pace and encouraging your input. I’m excited about the rest of my rotation here at Thamshavn and can’t wait to see what the trainee programme has in store for the future. As we say in Norwegian, vi blogges (catch you in the next blog post)!