- Magazine
- Material science insights
- What is the resistance level of silicone rubber?
What is the resistance level of silicone rubber?
What does silicone rubber resistance mean
It is tempting to begin a blog on silicone rubber resistance by stating that this highly versatile material can resist all challenges: thermal variations, harsh environmental conditions (precipitation, wind, UV rays, etc.), salt and chemical corrosion, vibrations, aging etc. But perhaps, it’s better to start by stating that the resistance features of silicone rubber are only relevant if they meet the specifications of manufacturers and the needs of end-users.
In this introduction, let’s just review some of the main resistance characteristics of various types of silicone rubber and why they are the material of choice for combining a wide range of features required for high-performance products.
The overriding property of silicone rubber is that it is an inert synthetic elastomeric compound that comes in a variety of forms (oil, rubber, resin, grease, paste, etc.) and so can be integrated into different processes and products. They are therefore present in sealants, adhesives, lubricants, medical applications, cookware and insulation, to name but a few applications. Silicone can be combined with ingredients such as carbon, hydrogen and oxygen and other elements to ensure the proper features for each application. Catalysts, cross-linkers, minerals or silicone fillers and other additives, also provide specific resistance features.
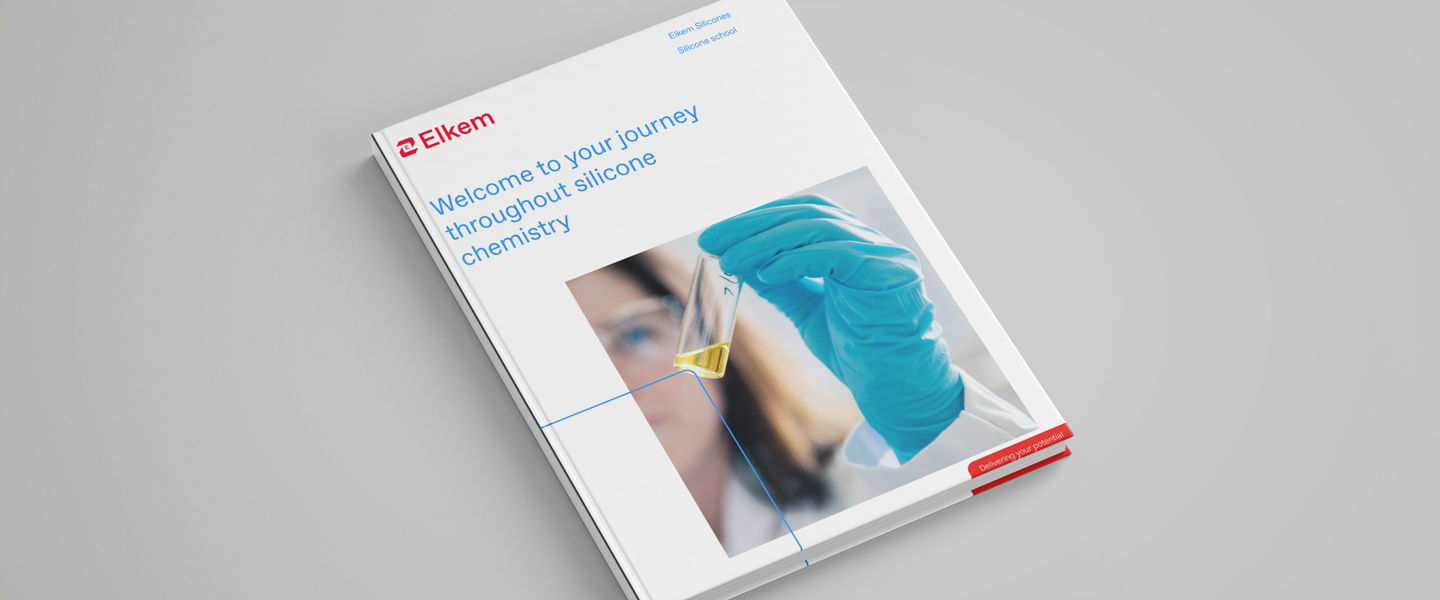
Here are some of the main silicone rubber resistance characteristics and how these apply to different requirements you may have:
- Thermal or temperature resistance, which is one of the most highly sought-after characteristics of silicone compounds, with the ability to adapt to extreme fluctuations in temperature, from -50°C to 250°C and beyond
- Varying degrees of flexibility, which means they can stretch or be compressed when pressure is applied and return to their original shape at variable speeds when pressure is decreased or eliminated
- High tear or tensile strength, closely linked to flexibility, which is the degree to which silicones can be stretched before breaking
- High stability against all forms of radiation, in particular UV rays, especially important in resisting extreme weather conditions and preventing deterioration and cracking, thus ensuring durable insulation and waterproofing
- Fire and flame resistance, particularly critical in applications where human safety is a must, such as places where people gather and closed environments, including transport vehicles
- Chemical resistance, which protects parts in contact with various types of corrosive products, once again particularly important in ensuring efficient and safe operations of equipment in direct relation with human activity and safety
- Reliable insulation and high-grade dielectric properties to resist the pressures to which electrical and electronic parts are submitted, ensuring coating, potting and sealing of components as well.

Silicone Rubber
HCR, together with LSR are also commonly known under the umbrella name of Silicone Rubbers
What are the underlying chemical characteristics that enable silicone rubber resistance?
The basic structure of silicones is made up of polyorganosiloxanes, where silicon atoms are linked to oxygen to create the «siloxane» bond. The remaining valences of silicon are linked to organic groups, mainly methyl groups (CH3): Phenyl, vinyl or hydrogen.
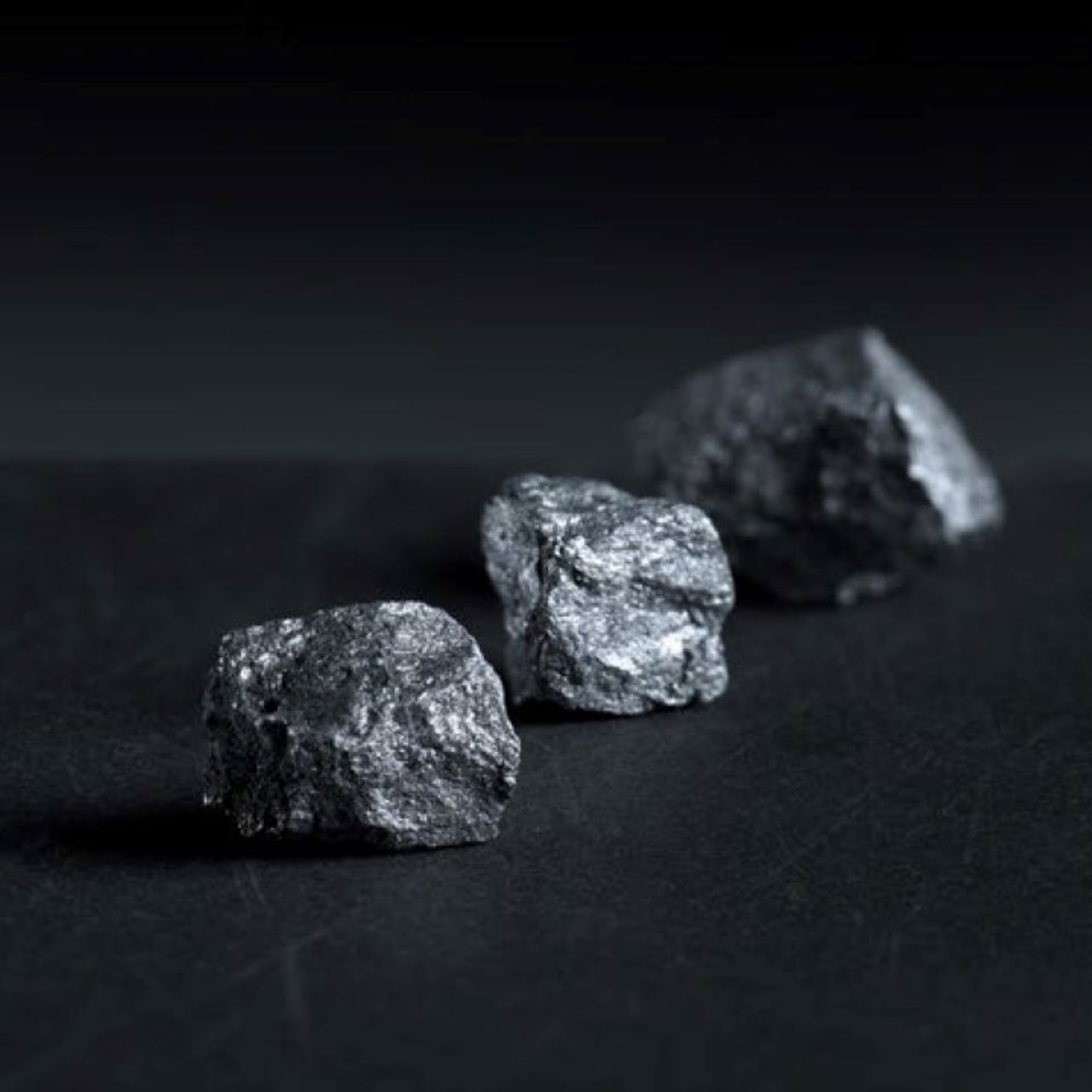
From quartz to silicon to silicones
This basic chemical structure is rendered more resistant to various pressures – heat variations, ozone and UV rays, hazardous chemicals, harsh weather conditions, mechanical pressure, etc. – through the addition of an almost endless numbers of various fillers, catalysts and other molecular enhancements.
Let’s take a concrete example: heat resistance. Silicones, by nature, are heat resistant because their formulations are based on Polydimethylsiloxane polymers (PDMS) which provide higher thermal behavior than organic rubber and thermoplastics. The Si-O energy bond is intrinsically highly resistant to oxidation (106 Kcal/mol) compared to the C-C bond (85 Kcal/mol) of organic rubber. This strength explains silicone’s high thermal stability (from -50°C to up to 250°C), as well as its resistance to oxidation, which together provide greater fire resistance.
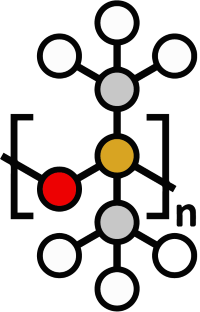
What are the main silicone rubber properties?
In this section, we examine in greater detail the main categories of silicone rubber properties, in terms of their main resistance features: mechanical, thermal, and environmental.
Mechanical Properties
Tensile strength
Tensile strength is the ability of elastomers, including silicone rubbers, to withstand stress (stretching and deformation) before their breaking or tearing point. Elongation at breaking point is expressed as a modulus in percentage terms. Silicone rubbers can typically withstand 100% to 300% modulus. Tensile strength depends on the characteristics of the rubber itself, the structures of its polymer chains and on the various additives and crosslinks in its formulation that will increase its resistance.
Silicone rubber is known for providing resistance at higher temperatures compared to organic rubber. It also can maintain its tensile strength in a high range of temperatures, from below -50° Celsius to over 250° Celsius.
Compression set and resilience
Compression set is defined as the ability of an elastomer to resist a decrease in thickness after the material has been subjected to pressure under certain conditions: load, time and temperature. Compression is expressed as a percentage. The lower the percentage, the better the quality of the material. Therefore, a compression set of 10% indicates that the material regains 90% of its initial thickness after prolonged compressive pressure at given temperatures and bend.
Once the elastomer is installed, the rubber’s resilience or memory over time increases. This is particularly important for the plugging capacity of elastomeric gaskets, seals or the protection provided by cushioning pads, for example. In silicone formulations, the key to a successful material is to find the right balance between compression set, tensile strength (or elongation at break point) and tear strength.
Resistance capacities
Elastomers must resist different types of aggression or pressure, including:
- Flex cracking, which is the ability to withstand numerous flexing cycles without producing surface cracks because of this stress. This is also referred to as flex-fatigue resistance, an important requirement for critical parts in transport and aerospace applications. Design engineers and technicians must find a unique blend which provides the right balance in silicone rubbers that resist flex cracking at variable temperatures (high and low), harsh environments, and repetitive cycles of duress without damage or deterioration for specific products or applications.
- Tear resistance (also known as tear strength), is the ability of a material to remain intact without ripping under great stress, technically defined is as the energy required to transforming a crack into a tear. It is closely connected to (but different) tensile strength, which is a measurement of the force required to pull something to the point where it breaks. Other factors, such as flex cracking, hardness, mechanical strength, and elongation are complementary measurements for determining the elastomeric properties of silicones. Silicone elastomers can be designed to integrate all these factors, since they are made with a combination of linear polymers, reinforcing agents, a crosslinker and a catalyst to achieve the right mix of mechanical properties. To increase resistance, including tear resistance, elastomers can be reinforced with mineral fillers, such as silica, alumina, calcium carbonate, silicone resins, etc. Radical condensation or addition crosslinking reactions may be used depending on the technology chosen to meet precise processing requirements. These characteristics are useful in a wide variety of applications, including architectural and heavy-duty textiles, electrical cables in energy production, building, transport, cooking ware, etc.
- Abrasion resistance is defined as the ability to resist mechanical actions such as rubbing, scraping or erosion which wear away surface material. Abrasion resistant elastomers are useful when moving and fixed components are regularly in contact between themselves, whether they are elastomers or other materials. Abrasion resistance is not necessarily a ‘natural feature’ of silicone, such as its generic tensile strength, tear resistance, aging or temperature resistance. However, abrasion resistance can be increased in cured silicone by the addition of reinforcing fillers, generating in turn a decrease in friction force. Therefore, depending on the application, technicians must choose the right grade of silicone elastomers and then find the right mix of silicone rubbers and fillers to achieve a balance between abrasion resistance and friction force. Abrasion resistance is particularly important in such highly exposed applications as tires or rubber coatings in mechanical systems such as gaskets.
- Impact resistance is defined as the ability of a material to withstand a shock with an outside force, such as a projectile. Silicone elastomers naturally provide impact resistance, with a ‘bouncing effect’ in most environments. For example, a silicone-based electrical protection cable or casing in a transport vehicle will withstand gravel or glass projectiles on the road. For higher levels of impact resistance in building materials, silicones and silicon-based microsilica fibers can improve the impact resistance of cements. In more demanding circumstances, such as ballistic armor, silicone is integrated into Hybrid Silicone Composites (HSC). This type of specialist formulation can enable the production of both soft and hard armor, useful in off-road building equipment, military vehicles or personal protection equipment.
Thermal and fire properties
- Thermal stability of materials in a wide temperature range (from -50°C to 250°C), impacting upstream process uniformity (excellent spread and coating capabilities) and reliable downstream operating performance in extreme temperature or environmental conditions
- Thermal insulation, to protect parts from overheating.
- Fire resistance of silicone rubber is obtained thanks to PDMS backbone and inert fillers, but fire resistance can be enhanced with selected halogen free additives, platinum and/or metallic oxides. During the burning of silicone rubbers, some volatile and cyclic molecules are produced with self-ignition near 450°C and are transformed into inert silica, H2O, SiC and CO₂. By consequence, low smokes emissions are nontoxic, non- corrosive and halogen free. This behavior allows a safe and quick evacuation of people during the event of fire.
Environmental properties
Silicone elastomers are used in high-performance applications, especially in harsh environments where other polymeric materials will fail. Parts made of silicone elastomer rubber ensure long durability and reliability, even when exposed to a wide range of temperatures (from -50°C to 250°C). They are also particularly resistant to extreme weather conditions and aggressive challenges, including:
- Ozone in the atmosphere, particularly present in certain geographical areas and in polluted urban environments, degrades certain rubbers (especially those that are polydiene-based) by reacting with main chain unsaturation, generating diminished surface strength, increasing cracking (referred to as dry rotting) and deteriorating performance and lifespan. Silicones offer much greater resistance than natural rubber polymers or ABS plastics, an especially important factor in sealing parts.
- Oxidation is one of the main factors in the aging of materials. Silicones offer very high resistance to oxidation and, in conjunction to its ozone and heat resistance features, is especially appreciated in sealing parts. RTV-1 silicones, for example have a chemically neutral curing system, guaranteeing no oxidation on contact with metals and so are intensively used in the bonding and protection of electronic components and other sensitive parts.
- Weathering is one of silicone’s best overall performance features. Silicones in different forms (pastes, coatings, sealants), are all largely unaffected by temperature changes, and therefore efficient in very different environments. Also, because they are water resistant and repellent (as well as resistant to oxidation), their protective layer offers long-term protection against all sorts of atmospheric pressure and aggression. If we use construction as an example – residential, offices or commercial –they all use minerals with variable porous surfaces. Being exposed to more severe environmental pressures than ever, due to climate, they need to be weatherproofed to avoid serious serious damage, including infiltration of moisture and dampness, formation of mildew and moss, loss of insulation, efflorescence or exposure to increased dirt pickup. Silicone, with is efficient water repellency features, reinforces structural protection and reduces water infiltration, and in some cases can also be formulated to improve soundproofing and thermal insulation
- Radiation is efficiently repelled by silicones which are largely unaffected by temperature changes, and therefore efficient in very different environments. As we have seen above, they are water and oxidation resistant. Add to this their resistance to radiation (up to 106 rad.) and their inertness, when in contact with numerous chemicals and microorganisms. For electrical and electronic applications, silicones in various forms also provide good electrical insulation, high dielectric strength therefore generate low levels of loss and, once again, protect against radiation. Silicone, by adapting to extreme fluctuations in temperature (from -50°C to 250°C) have high stability and therefore maintain their resistance to all forms of radiation, in particular UV rays.