- Material Science Insights
- From quartz to silicon to silicones
From quartz to silicon to silicones
The raw material quartz (one of the most familiar forms of silica) is the starting point for an array of materials with numerous uses in industry, research, and in the home. But how do we turn quartz into silicon, and from there into silicones? In this article, we’ll explore this chain of chemical conversions, and how they can be tailored to ensure the final product meets the demands of the application.
The silicon ‘value chain’
Silicon, with its unique properties as a semiconducting metalloid element, combined with its natural abundance on the Earth, has many roles in the modern world.
In its natural form as quartz (along with other forms of silica, as well as silicates), silicon has long been a fundamental component of materials used in construction, and the production of ceramics and glass, to name just a few. As the pure element silicon, it’s well-known as the main component of solar cells and integrated circuits, and perhaps less familiar as an aid to the production of metals and alloys.
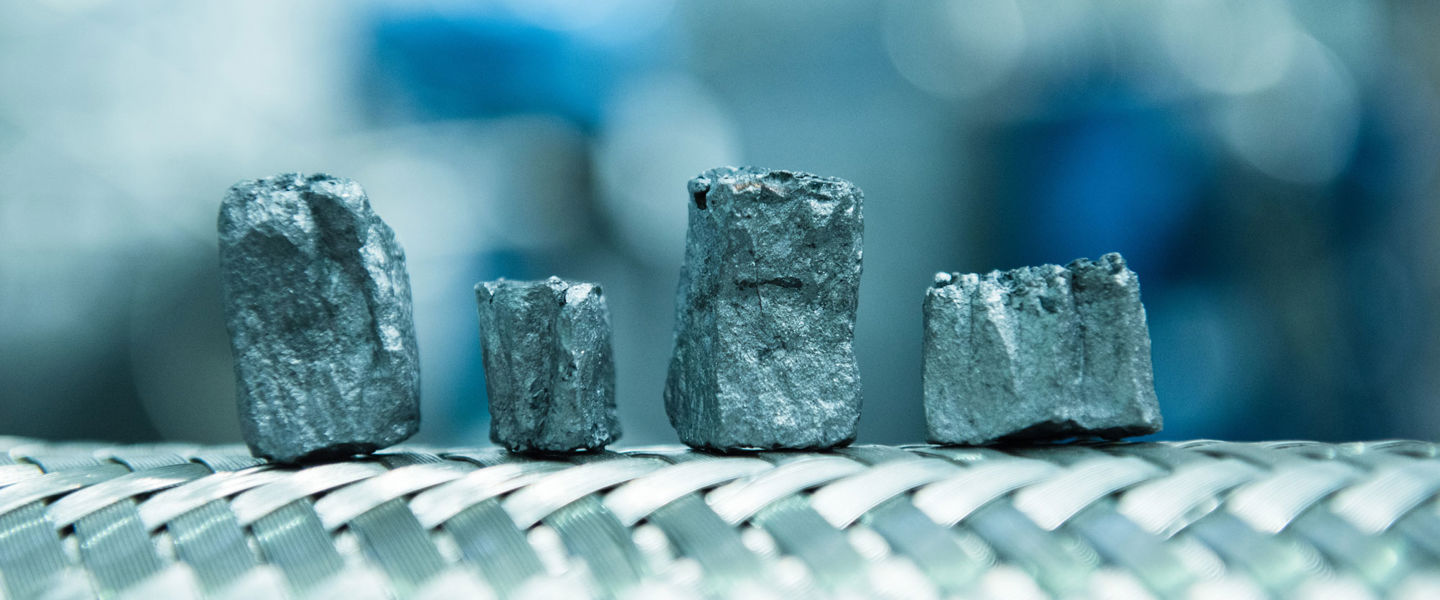
Silicon 101 - What is silicon used for?
But there’s more to silicon than just its inorganic derivatives – silicon’s ability to form covalent bonds to carbon as well as oxygen and metals opens up a wide range of organic compounds too. Prominent amongst these are silicones – synthetic polymers with a silicon–oxygen backbone, and an amazing variety of properties and applications, from cosmetics to sealants.
But how are all these materials made? It’s a striking thought that, numerous though these materials are, they all begin from just one mineral – quartz. So let’s take a journey from quartz to silicon to silicones, and along the way uncover some interesting transformations.
From quartz to silicon: How is silicon produced?
The strength of the silicon–oxygen bond makes silicon dioxide (silica) a rather unreactive starting material – and in fact this difficulty in releasing it from oxygen is partly the reason why pure silicon was only isolated in 1824.
Nevertheless, the natural abundance of silica makes it an obvious starting point, with high-purity forms such as the mineral quartz or the rock quartzite being commonly used. The first stage is always the production of metallurgical-grade silicon, followed by refining to higher-purity grades as needed.
Production of metallurgical-grade silicon
Metallurgical-grade silicon is produced from quartz by carbothermal reduction. This involves mixing the quartz with carbon-containing material (coal, coke, charcoal, woodchips) and heating it to about 1500–2000 °C in a submerged electric arc furnace.
The reduction takes place according to a complex series of reactions that differ between the inner (hotter) and outer (cooler) parts of the reactor. However, the overall scheme is as follows:
SiO2 (s) + 2C (s) → Si (l) + 2CO (g)
One of the intermediates formed in this process is gaseous SiO, which must be able to circulate through the reactor bed – either in order to encounter more carbon reductant and so produce silicon, or to leave the reactor bed to form silica fume (see boxed text). Other gaseous species evolved during the reaction must also be able to leave easily. For these reasons, the reaction mass must be porous – an impermeable mass would not lead to efficient production.
The crude silicon, which at this temperature is a liquid, is drained from the bottom of the furnace into a ladle, while more raw materials are fed in at the top. The tapped silicon is then refined to achieve the desired levels of aluminium and calcium, before it is cast into ingots of ‘silicon metal’.
How is silicon purified?
Higher-purity grades of silicon (those that are >99.99% pure), because of their use in electronic and solar applications, account for a growing proportion of global demand for the unalloyed element – so it’s worth looking at in detail.
The main method for the purification of silicon is the Siemens process. This first involves reacting it with hydrogen chloride (HCl), to produce the highly volatile chemical trichlorosilane (SiHCl3), which is then distilled. The resulting purified material then undergoes a process called chemical vapor deposition, involving decomposing it at high temperature in the presence of hydrogen gas. This causes silicon vapor to be deposited onto thin filaments of silicon, until it forms thick rods, which are then broken up.
An alternative process developed at Union Carbide converts the trichlorosilane to monosilane (SiH4), which is then deposited in a similar manner.
Production of monocrystalline silicon
All the methods of purifying silicon that we’ve mentioned so far produce silicon formed from lots of individual crystals (‘polycrystalline silicon’), but for silicon wafers used in electronics and (increasingly) for solar cells, single crystals of silicon are needed (‘monocrystalline silicon’). These are largely produced by the Czochralski process, which is favored because it can produce large crystals, and because it’s fast and relatively inexpensive.
The process starts with high-purity polycrystalline silicon, which is melted in a silica crucible, along with any dopants needed. A seed crystal of silicon is inserted into the melt, and then gradually pulled upwards and rotated, producing a cylindrical single-crystal ingot, with typical widths being 200 mm or 300 mm. Once cooled, this is sliced into wafers as needed.
From silicon to methylchlorosilanes: Adding functionality
In order to form bonds between silicon and carbon, and so allow later reactions towards the production of silicones to be controlled precisely, elemental silicon must be functionalized.
As in much of organic chemistry, halogens are ideal for achieving functionalization, and for silicon transformations, chlorine is preferred, with the main target compound being dimethyldichlorosilane, (CH3)2SiCl2.
The direct process for methylchlorosilanes
There are several ways of making dimethyldichlorosilane, but the most commonly used process (known as the ‘direct’ or Müller–Rochow process) involves treating silicon with chloromethane (CH3Cl, also known as methyl chloride), in the presence of copper as a catalyst. The basic reaction is as follows:
Si (s) + 2CH3Cl (g) → (CH3)2SiCl2 (g) + byproducts
The silicon used in the direct process is metallurgical-grade with low aluminium levels, and is first converted to a powder (<0.5 mm) using cone crushers and then mills, to increase the surface area and improve the speed of reaction. Following addition of copper (in the form of powdered copper, copper(I) oxide, copper(I) chloride or silicon–copper alloy), the reaction itself takes place at 250–330 °C and 1–5 bar in a fluidized bed reactor. The reaction generates a lot of heat, so to avoid ‘hot spots’, a strong flow of chloromethane gas is used to cause turbulence in the mixture.
As well as producing >80% dimethyldichlorosilane (as a proportion), this reaction also produces trimethylchlorosilane ((CH3)3SiCl) and methyltrichlorosilane ((CH3)SiCl3). Far from being unwanted byproducts, these compounds are desirable, because they are needed in the production of silicone polymers with different properties, as we’ll see in the next section.
Distilling methylchlorosilanes
Once the reaction is complete, the main challenge is then separating the individual chlorosilanes from each other. Because the main products are liquids, this is carried out by fractional distillation, usually followed by a second ‘fine’ distillation to separate dimethyldichlorosilane (b.p. 70 °C) from methyltrichlorosilane (b.p. 66 °C). This separation is important because even small amounts of methyltrichlorosilane can affect the quality of the silicones produced from it.
Higher-boiling residues are often further treated to extract more of the desired products and reduce waste.
The result of this process is a suite of purified methylchlorosilanes – vital in the next stage of the conversion sequence.
From methylchlorosilanes to silicones: Producing polymers
The dimethyldichlorosilane ((CH3)2SiCl2) that is the major product of the ‘direct’ process is next hydrolyzed to produce polydimethylsiloxane (PDMS) – the simplest of the silicone polymers (also known as polysiloxanes).
Hydrolysis of methylchlorosilanes
The basic polymerization process involves treating dimethyldichlorosilane with water, to replace the chloride (Cl) groups with hydroxyl (OH) groups, and so form the corresponding disilanol, (CH3)2Si(OH)2. A byproduct of this conversion is hydrochloric acid, which then immediately catalyzes the polymerization of the disilanols, producing polydimethylsiloxane, along with the elimination of water:
(CH3)2SiCl2 (l) + 2H2O (l) → (CH3)2Si(OH)2 (l) + 2HCl (g)
n(CH3)2Si(OH)2 (l) → [–Si(CH3)2–O–]n (s/l) + nH2O (l)
Tailoring the properties of silicones
As it happens, the production of silicone polymers does not use pure dimethyldichlorosilane, and this is where the other methylchlorosilanes mentioned earlier come in useful. The three main monomers are referred to in the industry as M, D and T units:
- M is the monofunctionalized monomer, trimethylchlorosilane or (CH3)3 Because it contains only one reactive group, it acts to cap a growing polymer chain, and so is used to produce shorter, lower-boiling silicones such as oils.
- D is the difunctionalized monomer,dimethyldichlorosilane or (CH3)2SiCl2. This is the main building block of all silicones, because it can bond to two other units, and so form long chains (or rings). When this monomer dominates, the products are soft solids or elastomers.
- T is the trifunctionalized monomer, methyltrichlorosilane or (CH3)SiCl3. Because this has three reactive groups, it is excellent at forming ‘bridges’ (cross-links) between polymer chains, and so is useful for making more rigid polymers such as resins.
As well as modifying the chain structure through the use of ‘M’ or ‘T’ monomers, the properties of the basic polydimethylsiloxane can also be tailored, either through changing the chain length, swapping the methyl groups with other carbon-based units, or by introducing additives to the final polymer. In this way, a wide array of silicone materials can be made, with applications as diverse as sealants, electrical insulators, lubricants and antifoaming agents.
Conclusions
From quartz to silicon to silicones, the production of high-value silicon-based materials relies upon a number of chemical conversions, carried out on a large scale globally. At Elkem we’re involved at all stages of this chain, from the extraction of quartz at our facilities in Norway and Spain, to the production of metallurgical-grade silicon, and its conversion via methylchlorosilanes to silicone polymers. This provides us with insights into all aspects of the ‘value chain’, meaning that we can adapt to new trends quickly without relying exclusively on third-parties.
And that adaptability will be needed more than ever in the years to come. The ever-growing use of silicon in electronics and solar technologies, combined with the versatility of silicone-based materials, means that the applications and scale at which silicon-derived materials are used will be constantly shifting as new technologies come on-stream. In fact, a nice example of the diversity of silicon-based products is the use of silicone adhesives to fix the power module to the back of silicon solar cells!
The good news is that using silicon-based materials can be coupled with a more environmentally-responsible approach, too. Because silicon comprises 28% of the earth’s crust, it’s a resource that is not going to run out any time soon. And although the process of converting quartz to silicon is energy-intensive, using renewable sources of energy can help to reduce the carbon footprint – just one of the ways in which we’re leading the field at Elkem.