- Magazine
- Healthcare
- How self-lubricating silicones improve the design of needle-less valves
How self-lubricating silicones improve the design of needle-less valves
Silicone-based needleless valves have many safety-related advantages but performance can be threatened by silicone’s unique self-healing ability. While a few solutions to this challenge already exist, each have their own limitations, so Elkem embarked on a mission with customers to develop something new.
Needleless valves are important components of safe vascular access systems for intravenous infusion and blood sampling. By eliminating the use of needles and allowing multiple usage, they reduce the risk of accidental needle-stick injury for caregivers, improve comfort for patients, and reduce the likelihood of catheter site infections.
“With needleless valves, catheterization is performed once and from there the valve is used to administer medication throughout the course of a day or week – however long,” says Michael Goglia, healthcare market manager, North America for Elkem Silicones.
“Once that IV is set up, it can be used to administer fluids, medication, or take blood through a new needleless valve. There’s also a benefit of less tissue trauma to the patient, lower risks of hematomas and reduction in needle anxiety, which is especially important in pediatric settings.”
Since the needleless valve part of the IV system is swapped out whenever a change in medication is needed, there’s also less reason for dangerous cross contamination to occur between drugs.
Silicone and the slit-healing phenomenon
Needleless valves are generally produced using silicone in conjunction with a plastic housing component. Silicone is often a go-to choice in the medical device industry due to important advantages like biocompatibility, chemical inertness, environmental stability, and high-performing physical properties. But it has also been associated with an important limitation in this application.
When silicone valves are produced, their septums are slit afterwards either robotically or manually to allow a controlled path for the fluids to pass through. However, when silicones are molded, the cure process is not 100% complete. Over time, and particularly after undergoing sterilisation, crosslinking of both sides of the slit can occur, resulting in the complete or partial closure of the slit. This phenomenon is referred to as ‘slit healing’ or ‘self-healing’ and can affect the functionality of the valve, posing a safety and efficiency issue in the care setting.
In some cases, a drop of fluoro-silicone oil is used to prevent this healing process and allow the valve to function normally, though this can be an expensive secondary step in the manufacturing process.
A better solution – self-lubricating silicones
A few years ago, Elkem Silicones set out to develop a better solution to this challenge, working in conjunction with customers to develop a range of self-lubricating liquid silicone rubber (LSR) materials. The Silbione™ LSR 4700 product line brings the same high physical properties as standard medical-grade LSRs with the addition of a self-bleeding lubricant acting as a barrier against the slit-healing phenomenon.
By introducing self-lubricating LSRs to this application, the tendency for the slit to heal post-production is greatly reduced and so is the need for secondary processing. This means less waste and less cost in post processing procedures.
The new solution also addressed some issues customers had been experiencing with existing competitor products.
“We had a customer come us to us with a problem,” says Goglia. “There are existing self-lubricating silicones that exist today, but they use far more oil within the formulation which bleeds out as they’re injection molded. What the manufacturer has to do is shut down production and then clean out the whole mold before they can produce more. It’s very costly in terms of downtime.
“Our material was designed to release the oil after molding. It's a delayed release structure which means you can mold the products, put them away, and then a day or two later the oil will start to come to the surface. It also uses less oil than competitive products today, so there's less free-floating oil that could potentially get into the environment or a patient.”
Performance benefits
The advantages do not stop there. Since these self-lubricating LSRs naturally have a lower coefficient of friction, the mechanical performance of the silicone valve in the plastic housing is improved.
Standard silicones by nature tend to be tacky at the surface, an effect that becomes more pronounced as the durometer of silicone rubber decreases. This can have a detrimental effect on the performance of the valve as it increases the force required for the silicone portion of the valve to slide against the plastic housing.
By switching from a standard LSR to a self-lubricating LSR, the coefficient of friction is greatly reduced, allowing for a more uniform force to move the valve. Self-lubricating LSRs can also be considered for other components that might benefit from a low coefficient of friction such as O-rings and seals. In most cases, the same tooling for a component made from a standard LSR can still be used.
Efficient manufacturing
Another unexpected benefit of self-lubricating LSRs was discovered in development of this line. Many times, the silicone valves are just a portion of an assembly. Often, when the final product is being assembled it typically employs the use of automated bowl feeders. Standard silicones can have a tendency to stick together in such an environment and either slow down manufacturing or contribute to scrapped parts.
By the introduction of a self-lubricating LSR into this process the parts feed far more easily and consistently, allowing for less down time in an automated assembly.
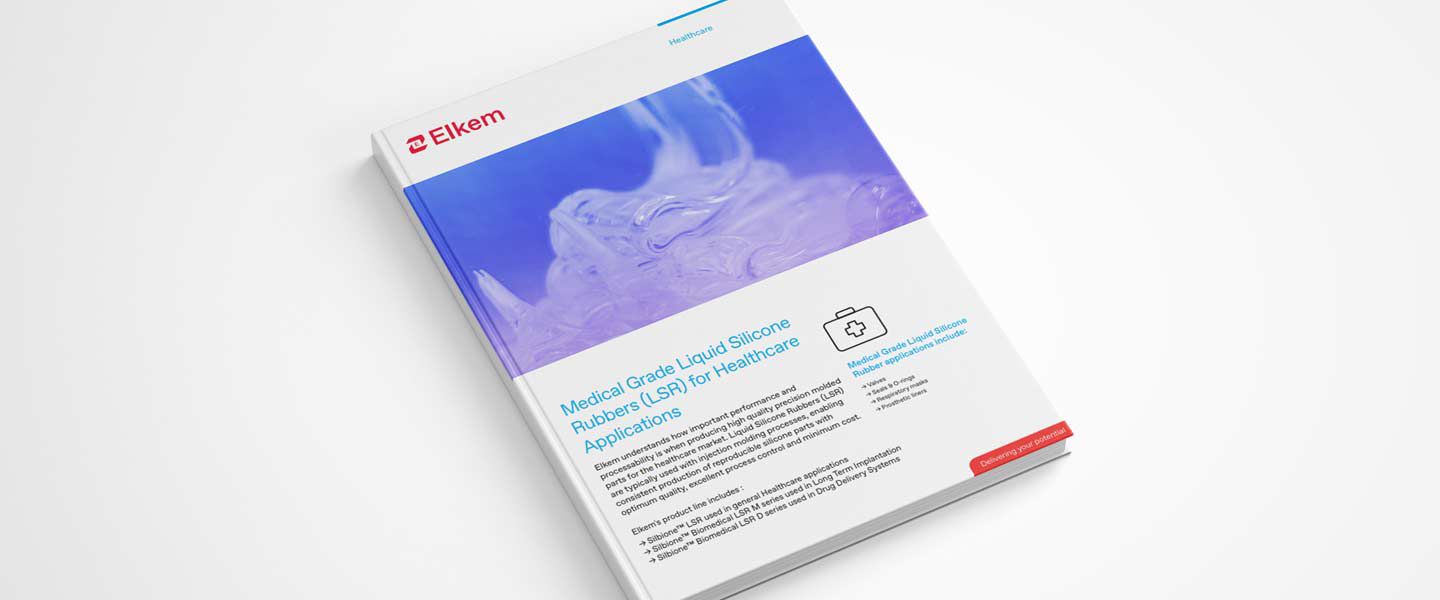
Medical Grade Liquid Silicone Rubbers for Healthcare applications
Discover our range of Medical- and Implant-grade LSR