- Trainee Blog
- After the calcining furnace
After the calcining furnace
Every day we are surrounded by millions of different products. Skin products, sun protection, spatulas, cutlery, mobile phones, electric cars, buildings, and bridges, the list goes on. All these things are readily available for you to buy or use, and in today’s day and age, you don’t even have to walk out the door to attain them. A couple of mouse clicks, and a package arrives at your door. But have you ever wondered where they all come from and what work lies behind all of it?
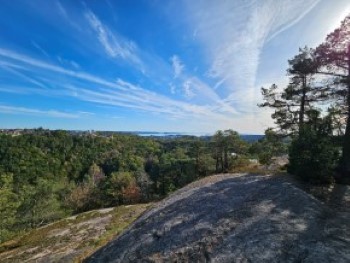
Before I started my first rotation in Elkem as a technical trainee I had a vague idea about what the company did. Production of silicones, silicon, and carbon solutions it says on the Elkem internet page. That to me sounded great and I was encouraged to apply for a trainee position. But where in our daily lives can we find these products? I personally don’t walk into stores looking for pure silicon or silicone materials, but since such products are being produced, there must be a market for it. What I quickly discovered during our onboarding programme was that there are traces of Elkem everywhere. Absolutely everywhere. Chances are that you will find traces of Elkem products in all the different things I mentioned in the first paragraph.
So, what is my role, a first-year trainee, in all of this? My first outplacement is with Elkem Carbon Global, and my day-to-day activities cannot be further away from finished handy smartphones and solar panels. In Elkem Carbon, we are producing electrodes, ramming paste and other carbon materials. Electric calciners with temperatures up to 2500-3000 °C are used to change the crystal structure of anthracite and green pet coke to give desired material properties. The calcining furnaces run day and night producing carbon materials essential for the production of our everyday products. In the same package CO2, off-gas and surplus heat is also created. And this is what my projects in Elkem Carbon so far have been about.
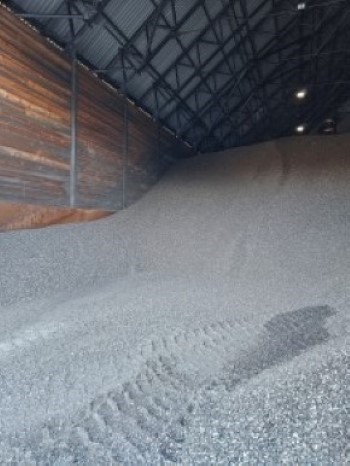
Off-gas consists of numerous components, some of which are not-so-good for neither you nor the environment. Before being released to the atmosphere it therefore needs to be incinerated. The presence of a flame atop a stack is a clear indicator that the calciners are operational, that is if incineration is the sole cleaning step. Although combustion removes some of the hazardous components of the gas, more can be done. At the Elkem Carbon plants in Norway and China they are doing exactly that. Namely further cleaning of the gas by removing dust, SO2, SO3, and NOₓ.
While this process may seem straightforward on paper, the reality is that there are countless solutions for gas cleaning, much like the endless possible morning routines. Not even within Elkem Carbon is this done the same way. Hence why my project is trying to benchmark the different off-gas cleaning facilities that we are currently using in Elkem Carbon. What are the similarities and dissimilarities and how can the plants learn from each other to improve their processes.
In addition to cleaning the off gas, there are other potential uses for it. The first step in the cleaning process is to burn it in a combustion chamber. This creates surplus heat, presenting opportunities for energy recovery. There is an abundance of technologies created for energy recovery purposes, but which ones are suitable for Elkem Carbon? That is also something I am looking into. In this ever-evolving field of technology there is much to learn and discover!
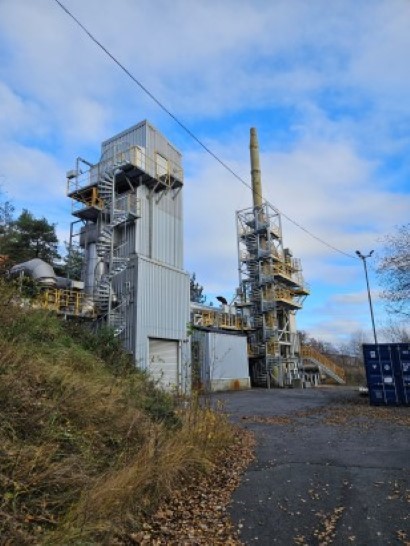
As I approach the midpoint of my first rotation in Elkem, I am looking forward to seeing how my projects will develop and transform during the last part of my first rotation here in Kristiansand. The trainee programme has so far not only taught me about the intricacies of the calcining process but also broadened my network. This includes connections not only within Elkem in Norway but also with Elkem plants worldwide. Despite being based in Kristiansand, I am regularly connected with colleagues around the globe through emails, meetings, and potential site visits.
Finally, while going from raw materials to finished products like sunscreen still hold some mysteries for me, there is no doubt that there are several complex processes happening behind the scenes before these items reach our shelves. The next time you use your smartphone or flip a pancake with your spatula, pause to consider the intricate processes behind their creation. Delving into the production process reveals a much unseen world of processes and might just surprise you with the complexity involved in crafting the everyday items we often take for granted.
With Christmas quickly approaching and winter settling in, I am excited for what Kristiansand has to offer and my continuation with the Elkem trainee programme!