- Magazine
- Trainee Blog
- Exploring the silicon value chain
Exploring the silicon value chain
After finishing my studies in chemical engineering, I was lucky enough to be chosen for the Technical Trainee program at Elkem. I figured this would be the perfect start to my working life, as I would be able to explore a lot of Elkem’s operations and figure out what I most enjoy working with. For the first 8 months I was located at Elkem Thamshavn in Orkanger, which is 30 minutes from Trondheim. This is a plant producing silicon with 99% purity, which is sold to various companies in the chemical and aluminium industry. Having just spent 5 years studying very theoretical subjects, I was eager to get some practical engineering experience!
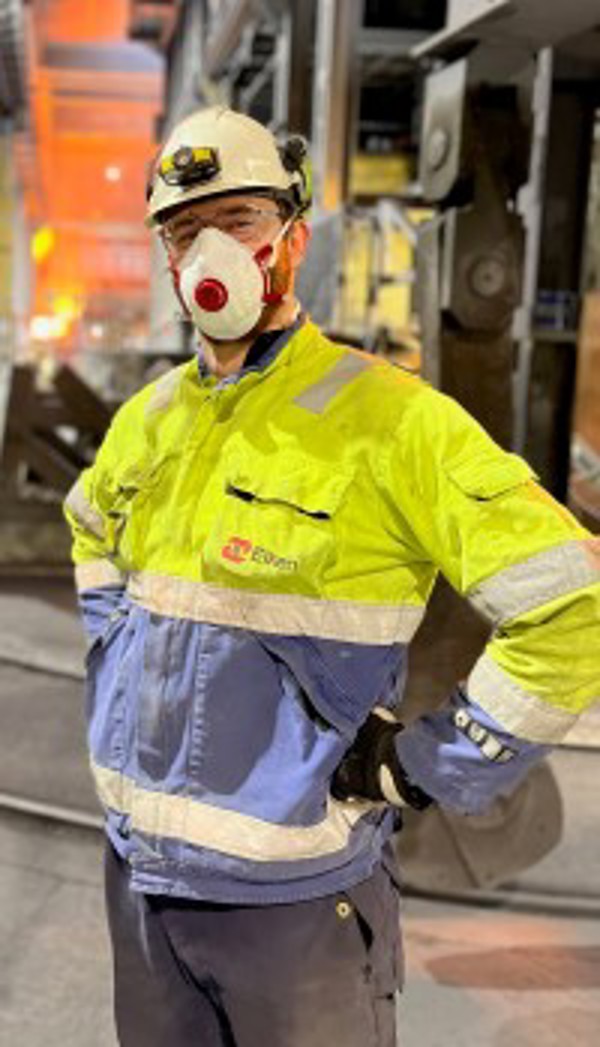
There was a steep learning curve starting work at a smelting plant. At university I had no subjects in electrochemistry or metallurgy, so I had to learn all about the process from scratch. In addition, I had to learn about all the other process areas needed to keep the furnaces running. Luckily everyone was very helpful and open to questions, so I felt I got up to speed rapidly.
Thamshavn has two furnaces, one which has a power usage of 44 MW and the other one 25 MW. For some scale of reference, 44 MW is approximately the combined electricity usage of all the houses in Trondheim, and this is the second largest silicon furnace in the world. The energy is used to heat up a mix of quartz (SiO2), carbon and wood chips to over 1800oC. At this temperature the carbon will “steal” the oxygen from the quartz, and you get silicon.
My tasks here were varied. I was initially supposed to work mostly on digitalization projects, but as time went on, I was more and more drawn towards tasks in production. Therefore, I got to work on both coding, data analysis, risk assessments of changes in the production process, coordination of work during maintenance stops and many other smaller tasks that need doing to keep the process going.
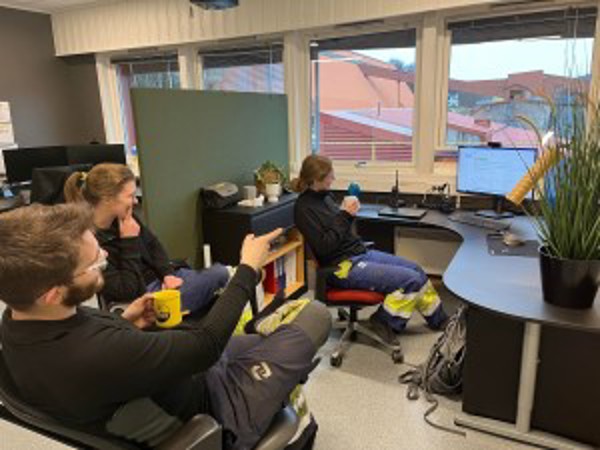
I worked closely with the process managers/metallurgists for the furnaces and got to spend a lot of time understanding how the process is controlled to both produce good quality products and operate safely. As I gained more experience, I occasionally got to be a substitute process manager when one of the others were away. My last two months here I worked full-time as process manager for the 44 MW furnace, as the actual metallurgist had to work on improvement projects. This was quite the challenge for someone barely out of university! Luckily, I wasn’t entirely alone and could discuss problems with the metallurgists and the production manager, and they always had good advice. My biggest learning point from this experience was how important your social skills are when working in production. A lot of your time is spent talking with operators and mechanics/electricians and communicating well and getting along with people is crucial to make sure everything runs smoothly. All in all, I learned a ton during my time at Thamshavn, especially while acting as process manager!
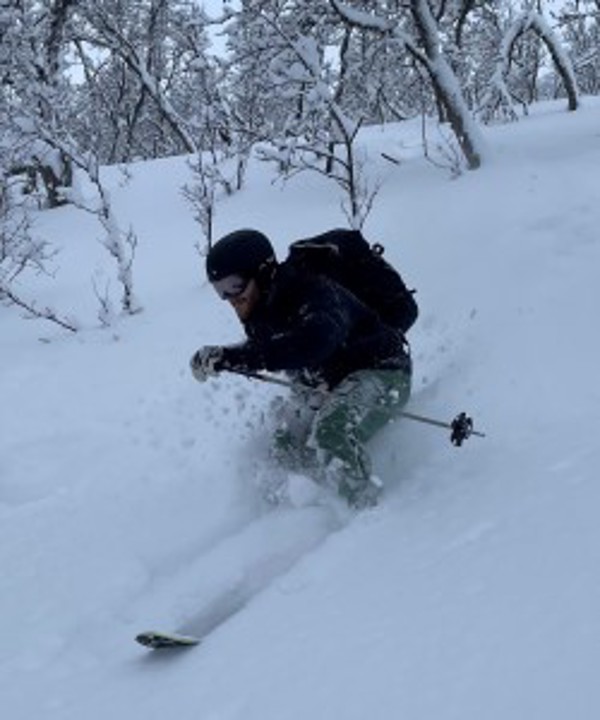
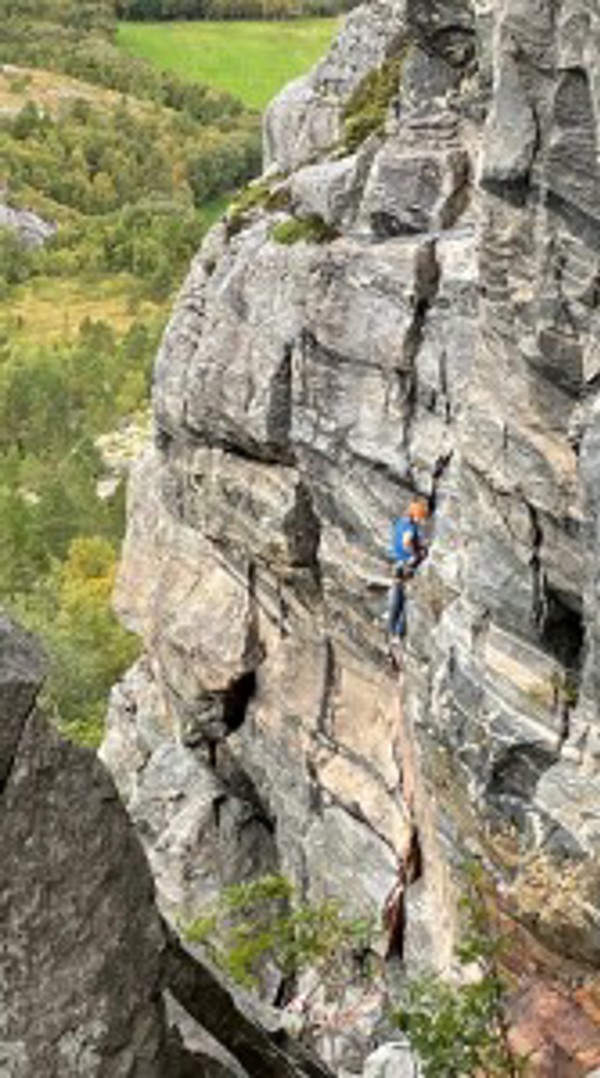
I lived in Trondheim during my period at Thamshavn, which is a great place if you like being active outdoors in your weekends. Before the snow came, I spent a lot of time climbing outdoors, the picture showing a trip I had to Flatanger with my colleague Caroline. She was recently a trainee herself, and you can still find her blog posts in the Trainee Blog page. During the winter I did a lot of ski touring in Storlidalen, which is one of the best areas in Norway. We also had weekly climbing sessions in Orkanger with a group from work, which was both fun and an opportunity to get to know my colleagues better.
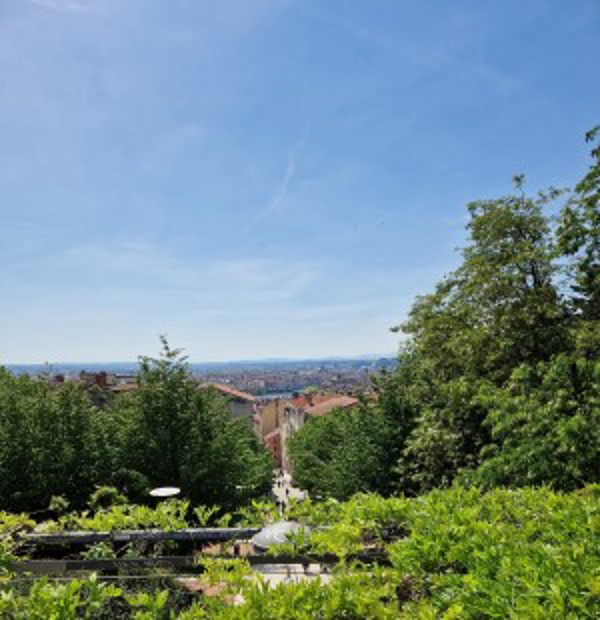
Leaving Thamshavn for my next rotation gives me mixed feelings. On one hand, it’s sad to leave a place I both enjoyed being and learned so much from, but on the other, my second rotation is in France, which is also very exciting! A lot of the silicon produced by the furnace I managed at Thamshavn is sent to a factory in Roussillon, which is just south of Lyon, and for my second rotation I have followed it downstream to learn how it is turned into silicone. Here, I am not working as closely with production, but with digitalization projects aimed towards the factory in Roussillon. One project is to make production data from the factory easier to visualize and access in morning meetings in production, so that they can see problems better and act to fix them faster. Another is work on predictive maintenance, where we use machine learning algorithms to watch live sensor data from the equipment and give warnings when they see indications of problems. This way we can discover failures in equipment at an early stage and have time to fix problems before they become worse. I recently also attended the Elkem Business System (EBS) University. This is a weeklong training course all trainees attend during their second rotation, where you learn good methods for working with problem solving, process management and many other useful things. Usually around 35 people from all over Elkem attend, so it’s also a good opportunity to get to know new people.
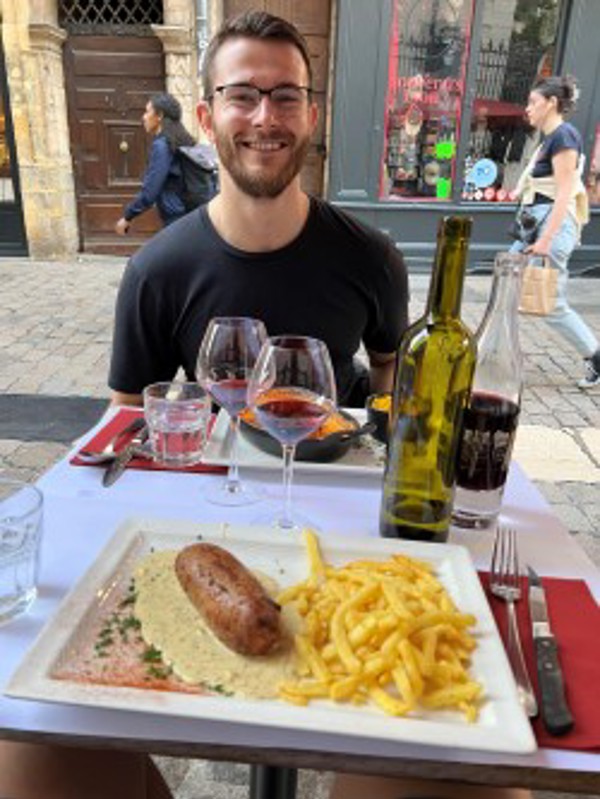
At the time of writing this, I have lived in Lyon for almost two months. We are two trainees here, and we have spent a lot of time exploring the city. Lyon is known as the food capital of France, and if you’re a food enthusiast it is a wonderful place to explore. They have a lot of local traditional dishes I hadn’t seen before arriving, like andouillette, which is a delicious sausage made from pork tripe. There are also other good restaurants from all over the world. The city of Lyon was established in Roman times, and you can see ruins from that time here still. It also has many charming streets and interesting museums, and I would highly recommend taking a trip here!