- Magazine
- Personal care and consumer goods
- The advantages of UV LED curable silicone release liners in the label industry
The advantages of UV LED curable silicone release liners in the label industry
Silicones have long been the preferred option for coating release liners for labels, but curing the precursors after they’ve been applied to the liner involves either heating them or using mercury-containing UV lamps. But this situation is now changing, with the release of silicones that can be cured using safer and more energy-efficient UV LEDs. So what do you need to know about this new technology? In this blog post, we take a look at UV LED curable silicone release liners, their advantages for label manufacturers, and the formats that we’re offering at Elkem.
For label applications from graphics to logistics, silicones have long been the favored solution for the peel-off liners. This is because their very low surface energy means that it’s easy to find adhesives that will detach from the liner with a slight force, yet adhere firmly to the target surface.
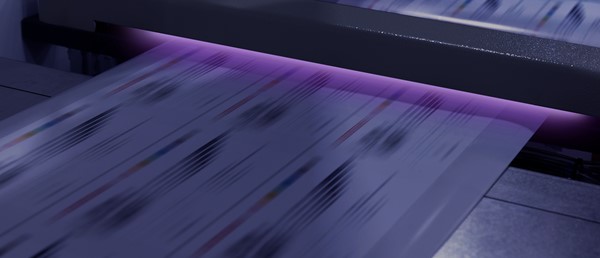
But up to now, one aspect of using silicone liners has always been a little tricky – converting the liquid precursors into the solid film of silicone on the substrate. Heat-based curing is a widely-used approach, but it comes with the problem of energy usage. Although solvent-based systems don’t need much energy input, they have obvious safety and disposal issues. Solventless technologies are an alternative, but they have considerably higher energy requirement, and for water-based emulsions the energy usage is higher still (because of the water that needs to be removed before curing)
UV curing does away with all these issues, and so is gaining interest in the industry – but it does come with its own challenges. The most significant one is that the UV lamps contain mercury, which is facing increasing restrictions for routine uses in many countries. The second is that these lamps use a lot of energy, as well as having other limitations related to conversion efficiency and the need for cooling, which is a problem for companies wanting to meet sustainability goals.
LED curing for UV lamps:
However, all these problems may soon disappear for good, with the advent of LEDs for UV curing of silicones. UV-wavelength LEDs have in fact been around for 20 years or so, but only now has the technology advanced sufficiently to make it feasible to use them for the large-scale production of silicone release liners.
The other key factor – and one we’ve pioneered at Elkem – has been the development of a portfolio of curing systems for silicones that works equally well with the narrow spectrum of light produced by a typical LED and with the broad-spectrum UV generated by mercury lamps. We’ve put a lot of effort into offering this dual-mode curing, because it means that manufacturers can transition from mercury lamps to LEDs over a period of time, rather than make the switch all at once.
Benefits of UV LED curable silicones
So what are the benefits of using this new technology for curing silicones? UV LEDs are:
- Safe and environmentally benign – Gone are all the safety worries about mercury
- More energy-efficient – Energy usage is about 50% less than that of mercury lamps
- Quick to use – They emit UV light instantly (no warm-up period)
- Operationally simple – They don’t need a reflector or any cooling equipment, and unlike mercury lamps they’re compact and not breakable.
- Long-lasting – They have a typical operational life of 20,000–50,000 hours, compared to about 2000 hours for mercury lamps.
So if your company’s focus is label production, there are plenty of good reasons to consider UV LEDs for curing your silicone liners.
How can UV LED curable silicones be used?
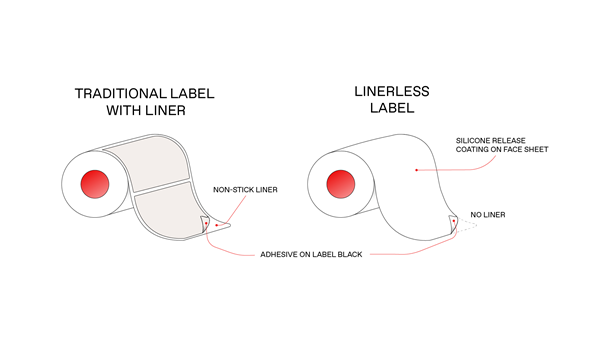
We mentioned above that UV LEDs emit a narrow wavelength of light. This means that the UV LED needs to be matched with a dedicated silicone precursor, to ensure that the wavelength generated is fully absorbed and used to cure the coating. It’s therefore good to know that there are UV LED curable silicone systems to suit all types of release liner applications – and at Elkem we’re ready to provide you with advice on what will work best for your application.
As well as ready-to-use silicones for regular super-calendered kraft, clay-coated kraft and glassine liners, we also offer silicone coatings for filmic liners. These are typically made from PE, PET or PP, and are useful where the liner needs to be durable, dimensionally stable, or resistant to chemicals or moisture. An important application of filmic liners is for medical/hygiene products, where it’s vital that the adhesive layer remains sterile.
Another hot topic at the moment is linerless labels, because they can contribute towards overall product sustainability by eliminating liner waste. We can provide UV LED silicones for these too, with options for both of the main methods of implementing this technology:
- Coat first: Used for the variable information printing (VIP) labels used in logistics and fast-food restaurants and point-of-sale applications, where the information is added using a heated printhead and a heat-sensitive facestock
- Print first: Used where silicone is applied over preprinted graphics to create linerless decorative and wrap-around labels.
A practical, sustainable option for liner coatings
As we’ve described here, the UV LED curable silicones we’ve developed at Elkem have a lot of potential for improving safety and speeding up workflows compared to existing mercury lamps. And with Elkem as the only supplier of UV LED curable silicone release liners for labels, now is a good time to get ahead of the market on what is sure to become a popular technology.
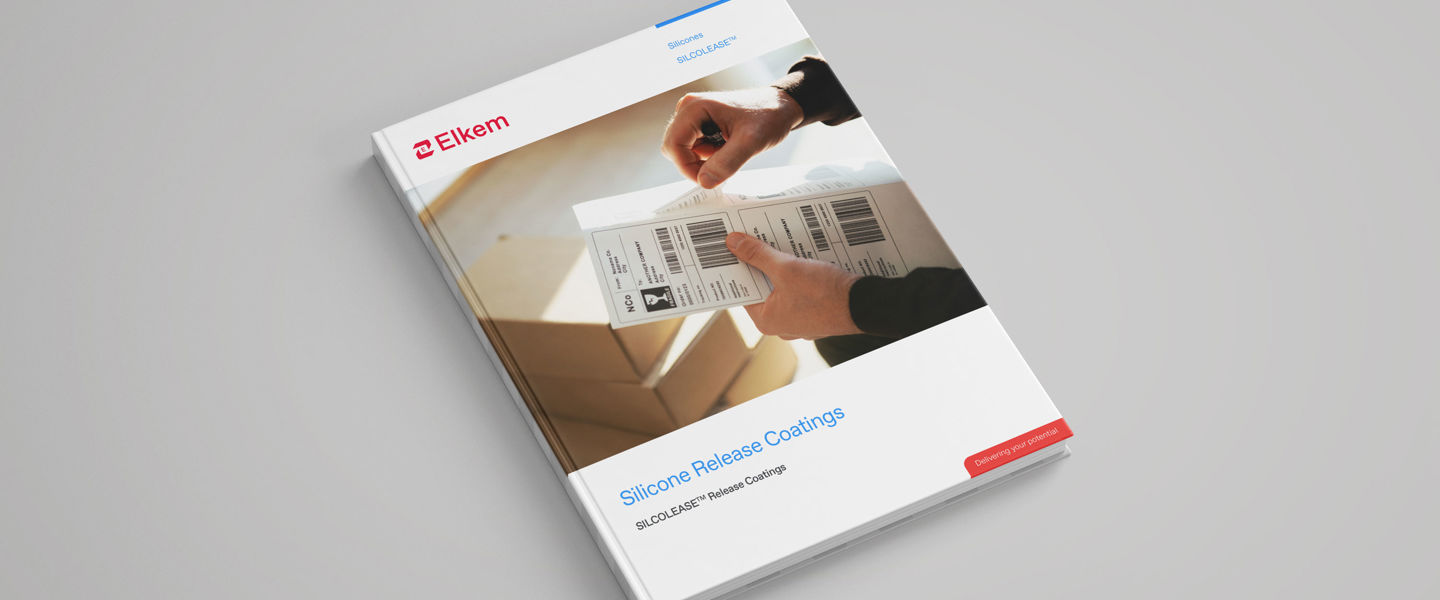
SILCOLEASE™ silicone release coatings
This guide will give you more information about silicones used for release coatings, and advice on substrate choice.