- Magazine
- Personal care and consumer goods
- An introduction to UV LED curable silicones
An introduction to UV LED curable silicones
Silicones are widely used as release coatings on liners for labels, tapes and other products using pressure-sensitive adhesives. However, up until now, the main ways of curing the silicone precursors after application to the liner have involved either heating or UV lamps containing mercury. But there’s a more sustainable alternative now available, in the shape of UV LED curable silicones. In this blog post, we investigate the science behind this innovation, and the advantages that the new LED-curable silicones provide for manufacturers of coated products.
Silicones have long been the ideal material to use when you need a non-stick coating on a paper or film. This stems from their very low surface energy and special viscoelastic properties, which allows most adhesives to be removed without difficulty. This property, plus the many ways in which silicone formulations can be tailored to the application, makes them the ideal material when it comes to coating the ‘liners’ (backing material) used for tapes and labels.
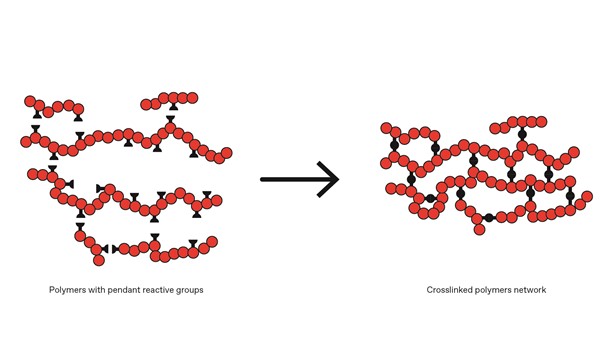
The challenge is getting the silicone onto the liner in a solid form. Relatively long-chain silicones used to be applied with the help of solvents, but these have fallen out of favor as manufacturers look to eliminate issues with safety and waste disposal. Water-based emulsions have emerged as a possible answer to some of these problems, but the energy cost of removing the water from the cured formulation is a drawback. A better approach is to synthesize the silicone polymer so that it has relatively short chains, which makes it liquid and therefore easily applied to the liner. The chains also contain reactive groups at intervals, which allows a curing step to be used to introduce cross-links between adjacent chains, turning the silicone into a solid layer.
What’s the best method for curing silicone coatings?
The question is, how do you carry out this curing step? One method that is still quite commonly used is thermal curing – basically, heating the coated liner to about 120–180 °C. But such high temperatures place limits on the substrates that can be used, and in addition, the formulations have to contain multiple components (including expensive platinum salts as catalysts). As a result of all these factors, the whole process is energy-intensive, which is obviously less desirable from the point of view of cost-effectiveness, carbon footprint, and sustainability in general.
A much ‘cleaner’ alternative to thermal curing is UV light, which offers the advantage of working with any substrate, and requires much simpler formulations (just the polymer and a UV-triggered initiator). This has in fact been a very popular method for curing silicones, but until recently, the only way of generating the UV light has been mercury vapor lamps.
![]() Picture of mercury vapor lamp
|
Mercury vapor lamps are effective and remain widely used, but they do have a drawback in the form of mercury, which is increasingly being restricted for routine uses in many countries. The lamps also generate a wide range of UV wavelengths, including the UVC that produces harmful ozone on contact with air, presenting another safety concern. In addition, as well as generating the UV wavelengths needed, they also produce heat, meaning that cooling equipment is needed for situations where they’re operating continuously (as in coating machines).
The development of UV LED technology for curing silicones
Light-emitting diodes (LEDs) that emit in the UV provide a solution to all these problems. They’re not completely new (they were invented in the early 2000s), but it has taken some time for the technology to be made suitable for industrial use – in terms of the wavelengths offered, their power, energy-efficiency and affordability.
The result is that although UV LEDs have been used in some simple non-critical applications (like printing inks), they are not yet in widespread use for curing ‘functional coatings’. These are applications where the properties of the cured coating needs to be finely tuned – which is exactly what’s needed for silicone release liners.
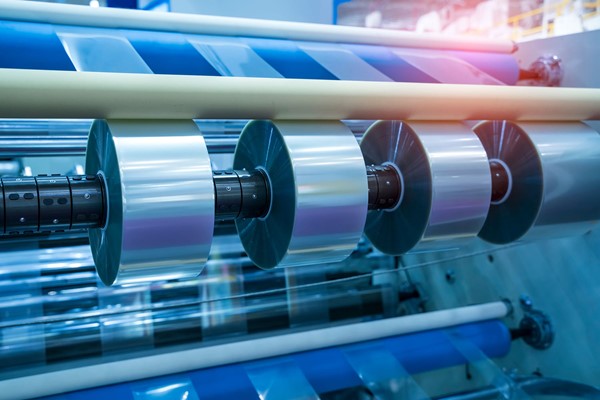
There’s also been another challenge to surmount in developing UV LED curable silicones for release liners, and that is finding the right initiator. Various chemistries are possible, but the one that is currently furthest advanced involves an initiator that releases radicals when hit with a particular wavelength of UV light. With mercury vapor lamps, a variety of initiators could be used, because the spectrum of light from these lamps is so broad. But with UV LEDs, the initiator needs to be carefully matched to the LED to ensure maximum photo-efficiency.
Dual-mode UV LED curable silicones
Fortunately, this particular challenge has now been overcome by our silicone specialists at Elkem, who have developed a radical initiator that is activated by 385 nm light from a UV LED, and which effectively cures an acrylate-functionalized liquid silicone. What’s more, this system also works with mercury vapor lamps, meaning that manufacturers can easily transition from one system to another.
And as shown in the figure below, there’s no compromise in terms of release performance, with release force, subsequent adhesion and extractables all on a par with results obtained using a mercury vapor lamp.
![]() Comparison of results for curing of silicone coating on a glassine liner run through our pilot coating machine at 100 and 200 m/min, using a mercury vapor lamp or a 385 nm LED – showing equivalent performance.
|
The benefits of UV LED curable silicones
The development of a practical UV LED curing system for silicone coatings offers numerous advantages compared to mercury vapor lamps:
- About 50% lower energy usage (partly because LEDs are ready as soon as they’re turned on)
- Proportionally lower running costs and CO₂ emissions
- No hazardous mercury
- No ozone release
- Compact and robust
- Operational life about 10× longer (20,000–50,000 hours)
- No cooling required.
This makes UV curing more practical and sustainable for numerous applications where silicone release coatings need to be applied. And as well as performing well for regular paper-based liners, the technology also works for linerless labels and filmic liners too – promising a future where clean, efficient and sustainable UV curing is used in a range of coating applications.
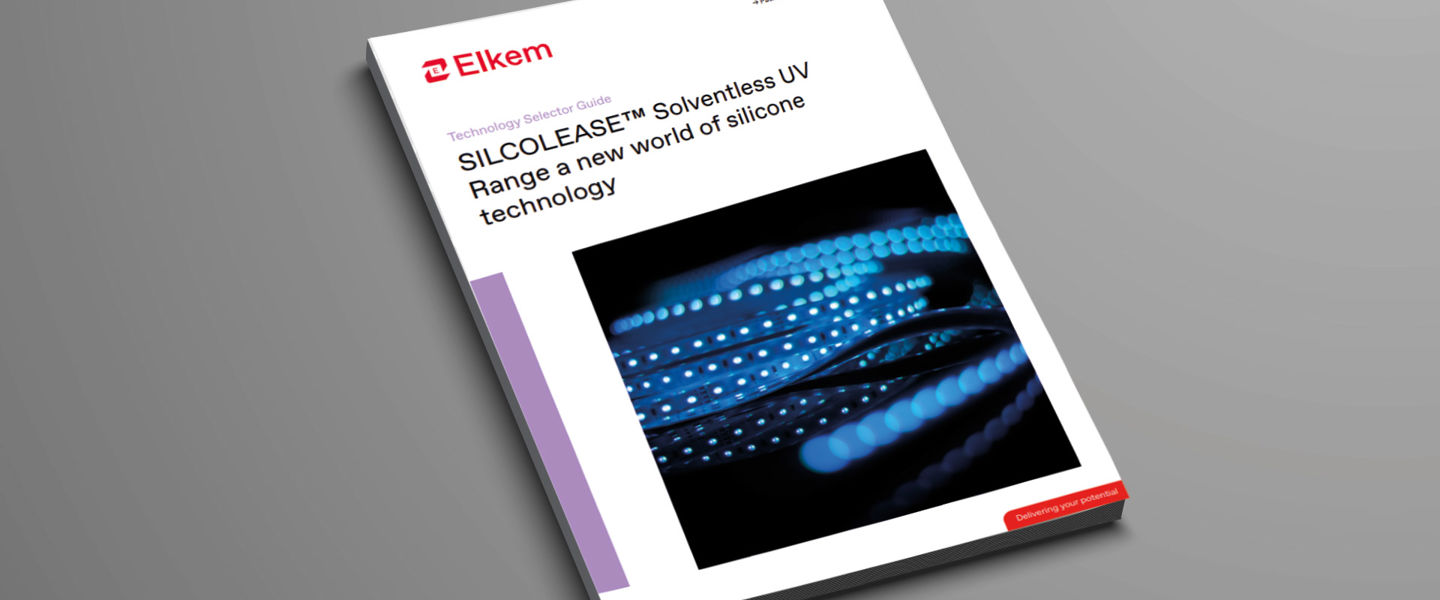
Discover the UV revolution with SILCOLEASE™
SILCOLEASE™ Solventless UV Release Coatings are safe functional silicones based on cationic or free radical chemistry well known to cure quiclky with UV Mercury Lamps , and from now on, with UV LED lamps within seconds.