- Personal Care and Consumer Goods
- How to Choose the Best Release System
How to Choose the Best Release System
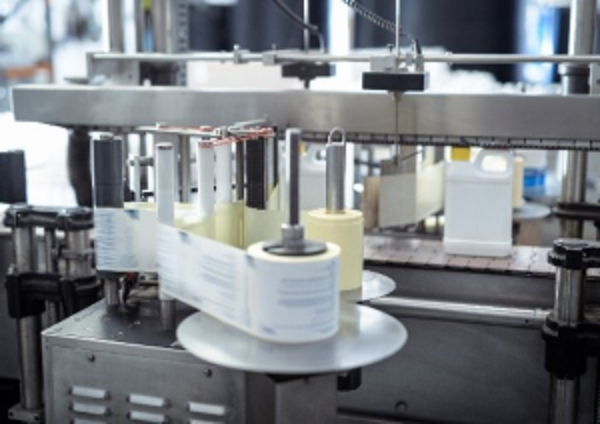
Emulsion release coatings offer many benefits in the silicone release coating industry. And while these products have been around for a long time, the actual benefits for using them can get lost over time, as technologies change and equipment modifications are made. Most of us carry a wealth of information and experience in our heads that we never take the time to document as we are “on to the next thing”.
So from time to time, it’s good to have a refresher on emulsion silicone release coatings and why they are as relevant today as they were 20 or 60 years ago
Background and Curing Importance
Silicone coatings are cured to form a filmic-like surface to prevent/reduce silicone contamination migration into the adhesive surface. This type of coating helps any tacky substance from sticking together or onto another surface until ready to be removed for end use, whether that’s an adhesive from a tape or label or a cookie from the cooking surface of a paper.
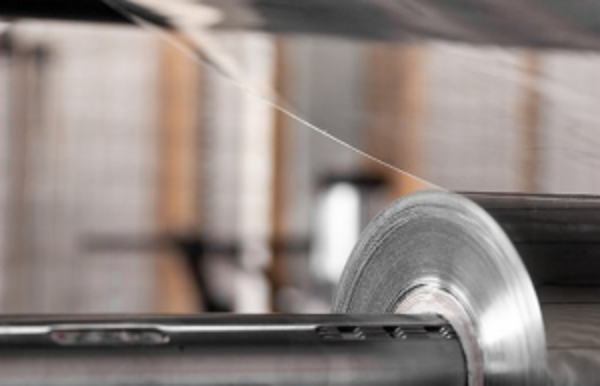
These curing methods can be achieved with (poly)addition or (poly)condensation cure methods. Condensation cures, when using a suitable catalyst, like organotin, are typically fast, inexpensive, and usually unaffected by chemical reactions with certain chemicals. This system can be difficult to control from a bath and working life stability. Addition cures, on the other hand, use a silicone hydride added across the vinyl (double bond) group and catalyzed with an appropriate catalyst, platinum.This system can endure higher curing temperatures, so you run faster line speeds, are easy to mix, do not produce by-products from curing. Inhibitors are used to prevent the formulation from catalyzing prior to use. The drawback to using a (poly) addition system is the need for an inerted environment (nitrogen replaces oxygen) when using ultraviolet light (UV) to cure the coating.
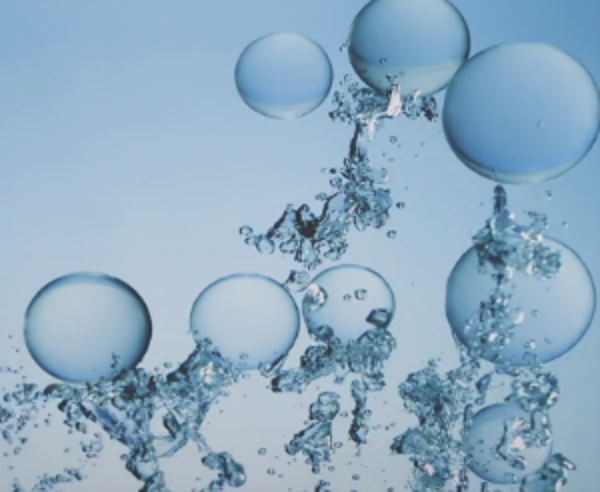
Wow! That’s a lot of chemistry! What’s the point to all this? Mainly to show that a release coating is more than just a silicone and a catalyst. There are many chemical reactions that occur in order to produce a low migration, well-cured filmic surface where adhesives do not want to adhere to the silicone surface. Understanding how these reactions occur and what happens with interactions between the silicone coating and the adhesive as well as the interaction between the release coating and the paper or film to which it has been coated onto is critical to achieve the best result for each application. Knowing the application process and end use of the label is as critical as understanding how the chemistry works. You don’t want a tight release for a high-speed labeling application and conversely, you don’t want your label to fall off the roll if you are labeling rolls or products by hand.
Now that we’ve briefly touched on components in a coating, let’s focus on emulsion coatings specifically. Emulsion coatings are basically 100% solids silicone products that have been dispersed in water and used as a coating. Using emulsions as the release coating system has many benefits:
- Emulsion release coatings, reactive silicone oils dispersed into an aqueous (water-based) system, eliminate VOC emissions versus the use of solvent-based coatings.
- Emulsion release coating formulations are easily modified to obtain a variety of release levels.
- These coatings are easy to modify and can be used to affect specific processing and performance properties.
- Coat weights are easily adjustable to achieve the proper level of coverage for a given application.
- Emulsion coatings are particularly suitable for applications on more porous papers.
- Clean-up is simpler than using harsh solvents.
- The flexibility of this coating allows application onto wide web substrates, inline on paper machines, inline on PET film extruder coaters.
- Application methods use common coating methods including Mayer rod, size press and gravure.
- From a regulatory perspective, silicone-based emulsion coatings are compliant for use in food packaging applications where other technologies may not have the same approvals.
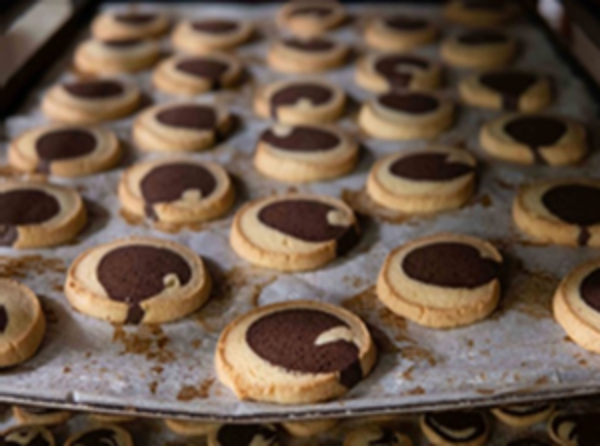
Release liners coated with an emulsion-based release system are an excellent choice for applications where flat, stable release is needed. Release liners coated with an emulsion-based release system are an excellent choice for applications where flat, stable release is needed. Emulsion coatings work well with most pressure sensitive adhesives, food packaging, and packaging applications where a non-stick area is needed. Silicone emulsion-based release coating systems help provide water repellency, endure high temperatures, are suitable for single and multi-use, and can be modified for variable release levels based on need.
So what system do you choose and how do you go about picking the right one for your release liner system and application? Many factors affect this decision.*
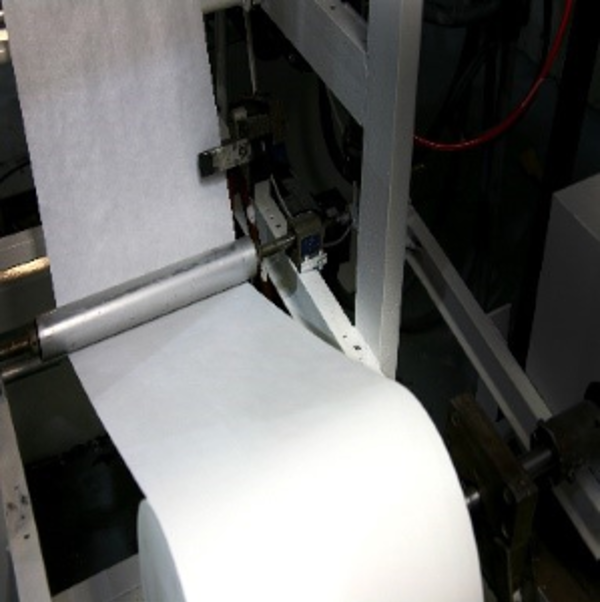
- Coating equipment and associated drying processes
- Line speed
- End use application
- Substrate to which the coating is applied
- Coat weight
- Type of adhesive
- Required release force
- Subsequent adhesion
- % Extractables
- Coverage
We have the experts who can help you find your potential and get the best system to meet your needs. Contact our TS experts to get more information and answer your questions. For more information regarding our Emulsion Release Coatings, please feel free to watch our Emulsions video.