- Magazine
- Personal care and consumer goods
- Developing more sustainable release liners using UV LED curable silicones
Developing more sustainable release liners using UV LED curable silicones
The performance and versatility of silicones mean that they are commonly used as release coatings on liners for labels, tapes and other products. However, curing the liquid silicone precursors after application to the liner usually involves either heating them or using mercury-containing UV lamps – neither of which are ideal from a sustainability point of view. In this blog post, we therefore take a look at new, more sustainable release liners that use UV LED curable silicones, and which promise to significantly reduce the energy consumption of the curing process.
Silicones, with their very low surface energy and unique viscoelastic properties, have been used since the 1960s for coating release liners for papers, tapes, and films. Thanks to their high performance and application versatility, they are still by far the most popular technology for the production of release liners used today – but in recent years the sustainability of the curing methods has come into the spotlight.
Approaches to curing silicone coatings
To understand the factors involved, it is first worth taking a look at the various approaches to curing silicone coatings that have been developed over the years.
The longest-established of these is to use a solvent to dissolve long-chain silicone precursors before application to the liner, but this is now rarely used because of the safety and disposal issues. An alternative idea is to use water-based silicone emulsions, but these have a different sustainability drawback, namely the energy cost of removing the water before curing the coating.
Yet another way of overcoming the need for solvent is to use shorter-chain silicones that are low-viscosity liquids at room temperature, and which can be applied as a solventless formulation.
But achieving greater sustainability is about more than just solvent, and this brings us to the question of curing. One approach is to use heat and a thermally-activated platinum catalyst, which remains a popular method in industry. However, the heating step incurs a significant energy cost, and platinum is expensive and increasingly difficult to source.
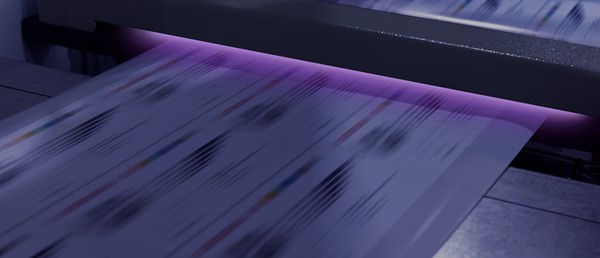
Alternatively, placing thermally-activated reactive groups along the silicone backbone allows curing to take place by the formation of bonds between the chains, but again comes with a high energy cost. Consequently, neither of these curing methods is particularly appealing for companies looking to reduce their environmental footprint or to keep costs down.
As a result, many manufacturers have turned to activation by UV light. This so-called ‘cold-cure’ technology was originally developed in the 1980s (along with silicone technologies adapted to it) to replace solvent-based silicone systems, allowing manufacturers to get the best of both worlds: curing with no solvent and no heat.
Engineering a more sustainable release liner
The story might have ended there, but at Elkem we realized that there remained one further way to improve the sustainability credentials of our silicone liner formulations, and that related to the source of UV light.
The conventional way of generating UV light for curing silicones is the mercury vapor lamp. These are effective and in common use, but the mercury they contain is increasingly being restricted for routine uses in many countries. That’s important enough in its own right, but in addition the lamps emit energy across a wide spectral range. This means that only a small fraction of the energy consumption is used to produce UV light of the desired wavelength, with an additional side-effect being that harmful ozone is produced because of the emission of shorter UV wavelengths.
To resolve this, we set ourselves a challenge – working out how we could adapt our silicone chemistry to make it suitable for use with UV LEDs. One problem was that, unlike mercury lamps, LEDs only emit a narrow band of wavelengths, which means that the curing chemistry used for the silicones needs to be precisely matched to the chosen LED.
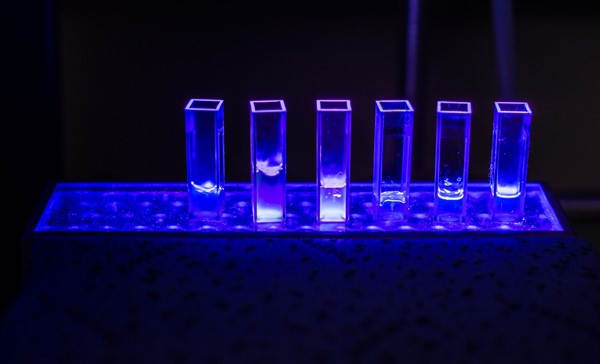
Tailoring the chemistry to the application
Thanks to our experience and skill in tailoring silicone chemistries, we successfully identified optimum silicone–LED pairs. The resulting formulations cured quickly and completely upon exposure to either 365 nm or 385 nm UV light from an LED, giving coating properties that matched those obtained with mercury vapor lamps, in terms of release force, subsequent adhesion and extractables. Importantly, the energy usage was also lower, with a 50% reduction found in our tests.
Following further optimization work, we now have solutions for a range of liner materials, including paper, filmic, and textile substrates. We also have a solution for linerless labels, which are increasingly popular because they add another dimension to product sustainability, namely, doing away with the release liner altogether, and incorporating the silicone onto the label facestock. The addition of the silicone can be done either before printing (in conjunction with a thermally-activated facestock and a thermal printer, as used in variable-information setups), or after printing (for decorative labels or wraparound labels).
UV LED curable silicones – The best choice for sustainable release liners
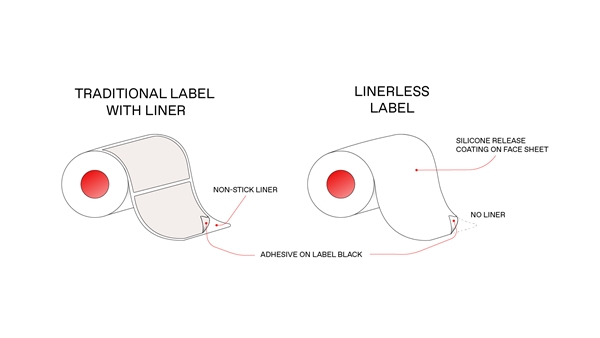
In summary, here’s how our UV LED curable silicones can help meet sustainability goals for the production of release liners:
- Energy-efficiency – UV LEDs use about 50% less energy than mercury lamps, meaning lower carbon emissions (and running costs)
- Lifetime – UV LEDs have a typical operational lifetime of 20,000–50,000 hours, compared to just ~2000 hours for mercury lamps
- Safety – UV LEDs eliminate health & safety concerns about mercury and ozone.
Furthermore, UV LEDs also offer some appealing practical advantages. They emit UV light instantly (without a warm-up period), they’re compact and non-breakable, and they don’t need a reflector or any cooling equipment. So if you’re looking to upgrade both your sustainability and operational performance for liner production, then UV LED curable silicones truly offer a bright future!
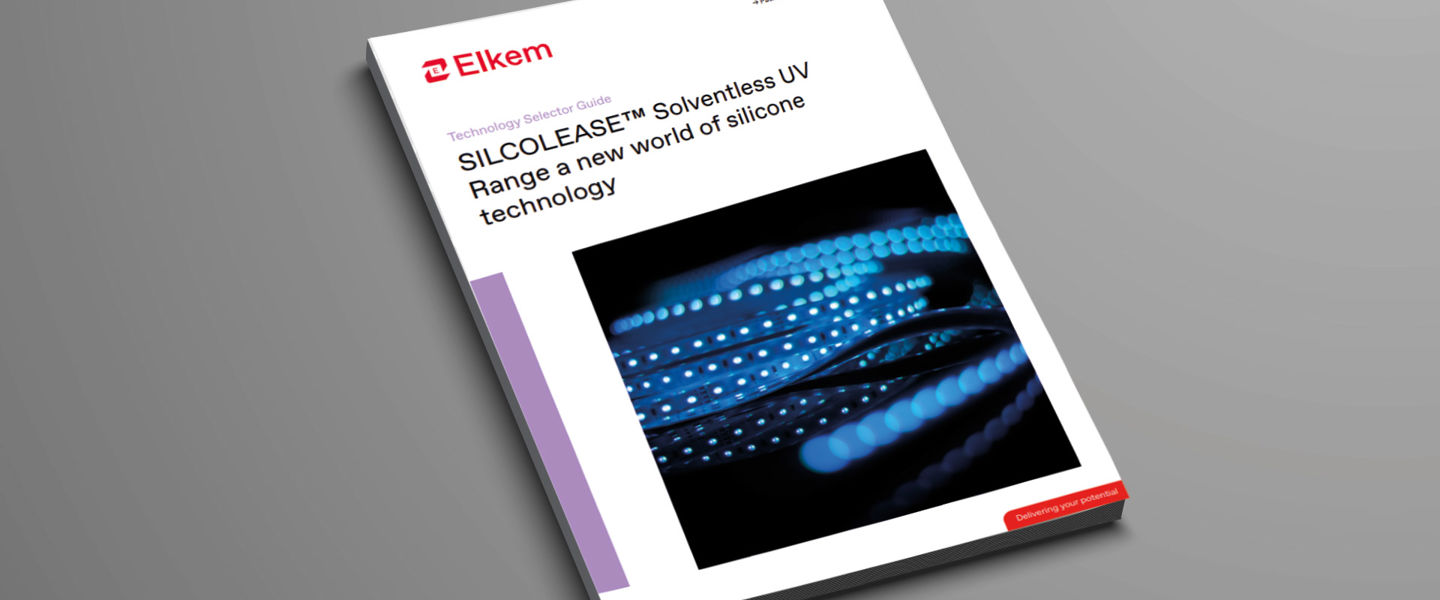
Discover the UV revolution with SILCOLEASE™
SILCOLEASE™ Solventless UV Release Coatings are safe functional silicones based on cationic or free radical chemistry well known to cure quiclky with UV Mercury Lamps , and from now on, with UV LED lamps within seconds.