- Magazine
- Trainee Blog
- Carbon, cake & Cognite
Carbon, cake & Cognite
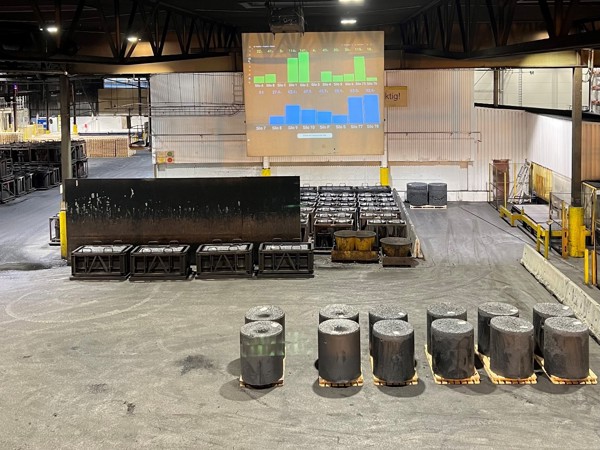
Since high school, I have been convinced that research and development was the path I wanted to proceed after university. This conviction was further strengthened by summer internships at the lab and during experimental work on my master’s thesis. However, after six months as a trainee, working closely with the production of carbon products, I have been converted to a production guy. Never had I thought that silo levels, feeding rate of a furnace, or real production compared to the plan could be so engaging. And who would have thought that using half a week to find the best way to display the specific energy consumption of a calciner could be so much fun!
I have had my first trainee rotation at Elkem Carbon Fiskaa, 30 minutes from my hometown. The carbon division in Elkem is most known for producing Söderberg electrode paste for use in silicon furnaces amongst others. However, they also produce cold ramming paste for use in furnace linings and recarburizer used in iron production. The plant is placed at “Fiskaa teknologipark” together with Elkem technology, Vianode, and REC solar.
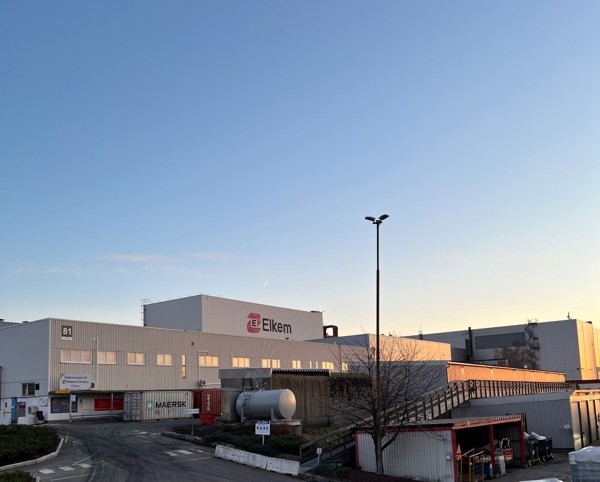
On my second day in Carbon, I joined my new colleagues for a two-day workshop. These two days were filled with brainstorming and discussion of use cases where the data displaying and machine learning tools from Cognite could be used. The use cases were to be used in a data-driven visualization project with Cognite. As this project was an upscaling of a previous proof of concept project, most of the people attending knew just as little as I did about the platform and programs. It was nice to be able to follow the project from the beginning and be trained together with the rest of the team instead of entering late. The first few weeks were mainly used for training in the different Cognite programs. One of my main tasks thereafter became to develop dashboards for different small projects and process lines.
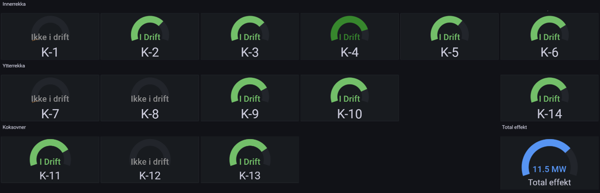
After 6 weeks in Kristiansand, I got the opportunity to substitute as process manager for the Elgraph production. Elgraph is a recarburizer used in the manufacturing of cast iron to adjust the carbon content. It is made by heating green pet coke in an electrical calciner to remove impurities and ensure maximum crystallinity. As a newly graduated, my experience and knowledge of process follow-up and making production plans was approximately nonexisting. Luckily the plant is full of knowledgeable process operators and process managers. I found myself discussing the process for hours with the operators, in addition to some detours to fishing, food, and the production of firewood.
The combination of process manager tasks and dashboard development was very useful for a better understanding of the processes. By getting to know the different components of the process, it was easier to understand what to display and which dashboards were useful. The dashboards then increased my understanding of production bottlenecks and helped me troubleshoot the process.
Fortunately, work is not the only thing to experience as a trainee. If you are as lucky as me, you might have the opportunity to experience the fantastic weather, as well as its wonderful archipelago in the south of Norway. Since my family is living nearby, most of my spare time in the fall was used for lobster fishing and cabin trips. I also became extra interested in baking cakes during my time in Kristiansand. This has been a delight for my cake-loving colleagues, as well as a frustration for my dietary-conscious colleagues. However, there is no doubt that it has given me some goodwill with the operators, making my many questions and requests more tolerable.
The carbon division, though relatively small, is an interesting division that I am grateful for having experienced. Soon my journey in Elkem will continue in Roussillon in France. I will collaborate with another trainee (Mats) on a digitalization project there. Hopefully, I can use some of my new knowledge from the Cognite project. However, the days in France will likely be less centered around daily production, and more affected by historical production and digitalization tools. I am looking forward to my next rotation but hope to get the possibility to work as a process manager again later.