- Magazine
- Material science insights
- What is the silicone rubber extrusion process?
What is the silicone rubber extrusion process?
Silicone rubber extrusion is a continuous process, in which a catalyzed compound (generally continuous strips) is introduced in the feeding system, with a screw carrying the material into the die. Pressure and temperature rise near the die to achieve the required viscosity level. The screw is the key mechanism in the process for extruded rubber since it feeds and compresses the material upstream so that it enters the die properly. The screw, once again, plays a key role at the output of the rubber silicone from the die, ensuring the quality and regularity of the profile being produced and avoiding the formation of unwanted bubbles or non-homogeneity in the final product. This is done by varying both the geometry of the screw, its speed, its pressure, and temperature, as well as other mechanical parameters. The profile then passes through an oven that cures the part. There are different types of ovens or kilns to carry out the curing process, mainly to adapt to different catalysts used in the compound. The temperature, pressure and the speed are adapted to the extruded rubber material.
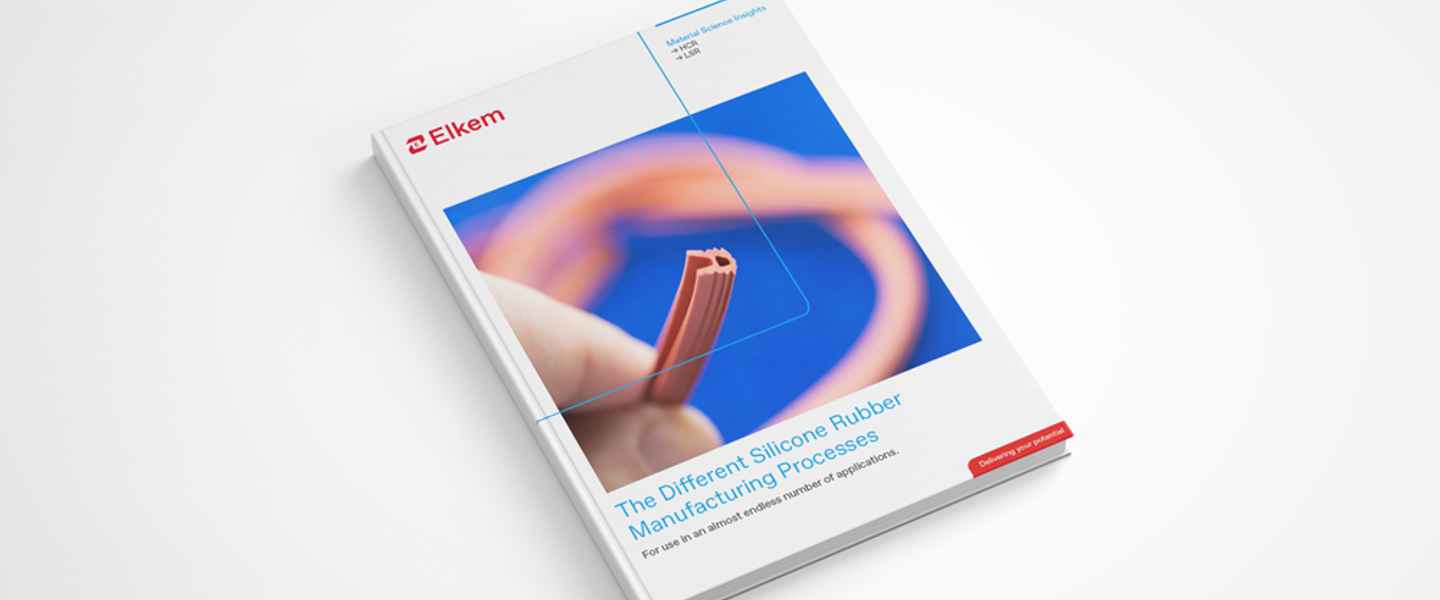
EBOOK - The Different Silicone Rubber Manufacturing Processes
For use in an almost endless number of different applications.
In simple silicone rubber extrusion, a single material is forced into a die, as described above. Coextrusion is a more sophisticated process in which two or more compatible polymer materials are extruded simultaneously in multiple extruders and then fused to produce multilayer structures, such as cables, pipes, panels, sealing mechanisms, etc.

The main challenge for manufacturers using silicone extrusion or coextrusion techniques is to choose the right grade of silicone rubber raw materials that will be compatible and perform best in their specific mechanical and temperature-controlled processes, thus enabling the final products to meet specifications, tolerance criteria and comply with regulatory standards. Silicone rubber can be used in different rubber extrusion processes and curing systems to achieve different features.
What are the applications and advantages of the silicone rubber extrusion process?
In terms of applications, silicone rubber extrusion is one of the most-widely used manufacturing processes, generally to make longer parts such as hoses, and cords, as well as complex profiles and cross-sectional parts, often combining multi-layered materials using complementary elastomeric or reinforcement components. Extruded parts are used to make large-scale and heavy-duty parts for industry, such as oven seals, electrical cables, wire insulation and seals. They are also used in home applications, such as food-grade piping or in medical applications such as drains and catheters.
Silicone rubber extrusion products and parts are also particularly appreciated in applications where shape stability and mechanical strength must be maintained in extreme weather conditions or harsh environments.
To succeed in achieving the required results using silicone rubber extrusion, several parameters must be respected:
- Accurate and robust dies
- Appropriate screw and line speed, tension and motor power
- Proper dimensioning, length aspects and ratios
- Carefully calibrated extrusion speed, pressure, and temperature controls from the upstream preparation of the material to the die through to the curing phase, including cooling
- Oven temperature, extrusion speed and pressure in the nozzle are key parameters to achieve the right balance between productivity and quality. Among other parameters, quality of the final parts is achieved by reaching a complete reticulation of the silicone
- Careful composition of critical materials, including tensile strength, fire resistance, chemical compatibility, food or medical grade compatibility, etc.
The main advantages of extrusion include:
- Efficient and economical and processing
- Minimal waste and, for many applications and very little post-process treatment
- Cost-effective and productive for large batches of continuous series
The main advantages of silicone rubber
- Different curing systems can be used depending on the oven chosen (room temperature, hot air, salt-melted baths or steam)
- Easily colored silicones, as well as varying degrees of transparency, important for aesthetic reasons, but also for identification of different types of tubing or insulation in complex assemblies