- Magazine
- Material science insights
- What is silicone rubber made of?
What is silicone rubber made of
What is silicone rubber?
Silicone rubbers are elastomers (which as the name implies, are flexible materials) made from a combination of linear silicone polymers, reinforced by different agents (most often carbon, hydrogen or oxygen), a crosslinker and a catalyst. An elastomer is characterized therefore by its ability to stretch or be compressed when pressure is applied and which returns to its original shape at variable speeds when the pressure is decreased or eliminated.
Silicone rubbers thus offer varying degrees of viscosity and structural features based on how the basic straight-chain silicone polymer has been combined with the processing temperature: Heat Cured Rubber (HCR), Liquid Silicone Rubber (LSR), and Room Temperature Vulcanization (single component RTV-1 and double component RTV-2). Depending on how these elastomers have been reinforced, (e.g., mineral fillers or silicone resins) they will offer different properties suitable for different applications, such as degree of flexibility, tear strength, temperature resistance, etc.
Silicone rubbers can also meet a wide variety of precise processing requirements in that many additives can be added to the elastomer in its final composition to ensure specific characteristics for end users, including color, fire resistance, demolding or chemical adhesion to aggressive outside elements, ensuring high performance standards for different applications.
They can be used for an almost unlimited number of applications depending on their formulation, from automotive and other transport vehicles to products for the home such as cookware, outdoor equipment such as footwear or sports gear, medical or food-related products, etc.
How are silicone rubbers synthesized?
Basically, silicone rubber synthesis is achieved in a three-step process:
- The preparation of chlorosilanes through the reaction of silicon powder (extracted from natural silica) and CH3CI or methyl chloride gas. The chlorosilanes produced are the building blocks to make silicone substances, each of which provide a hydrolysis reaction that enables the length and branching of the polymer molecular framework to be controlled. The three types of methyl chlorosilanes obtained during direct synthesis, which are then used to produce silicones are: trimethyl chlorosilane, dimethyl di-chlorosilane and methyl trichlorosilane.
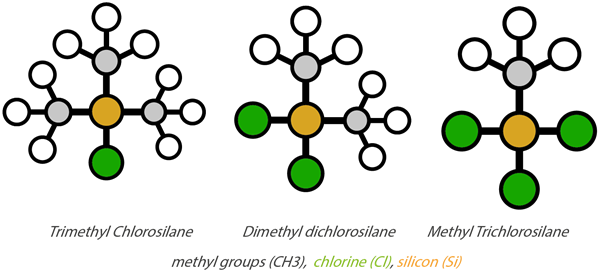
- The next stage is the hydrolysis and polycondensation of the chlorosilanes, which results in the making of basic silicone products: oils, gums, and resins. Oils and gums are straight-chain fluid compounds of various viscosities. When their viscosity increases to the point of solidifying, they are considered as gums. Oils, gums and resins can then be further processed to obtain various characteristics, working on their molecular framework based on the different groups of their original chlorosilanes.
- The last stage to obtain silicone elastomers is polymerization, which uses basic silicones compounded with reactive, straight-chained molecules, a cross-linking agent and reinforcement to achieve the desired mechanical properties (elasticity, absorption, tear strength, etc.) and safety features, such as insulation capacity, resistance to chemicals and flames, etc. Silicone Rubber is one type of silicone made from reactive silicone gums (straight chains with very high molecular weight) containing various reactive groups, mainly combinations of methyl, phenyl and vinyl.
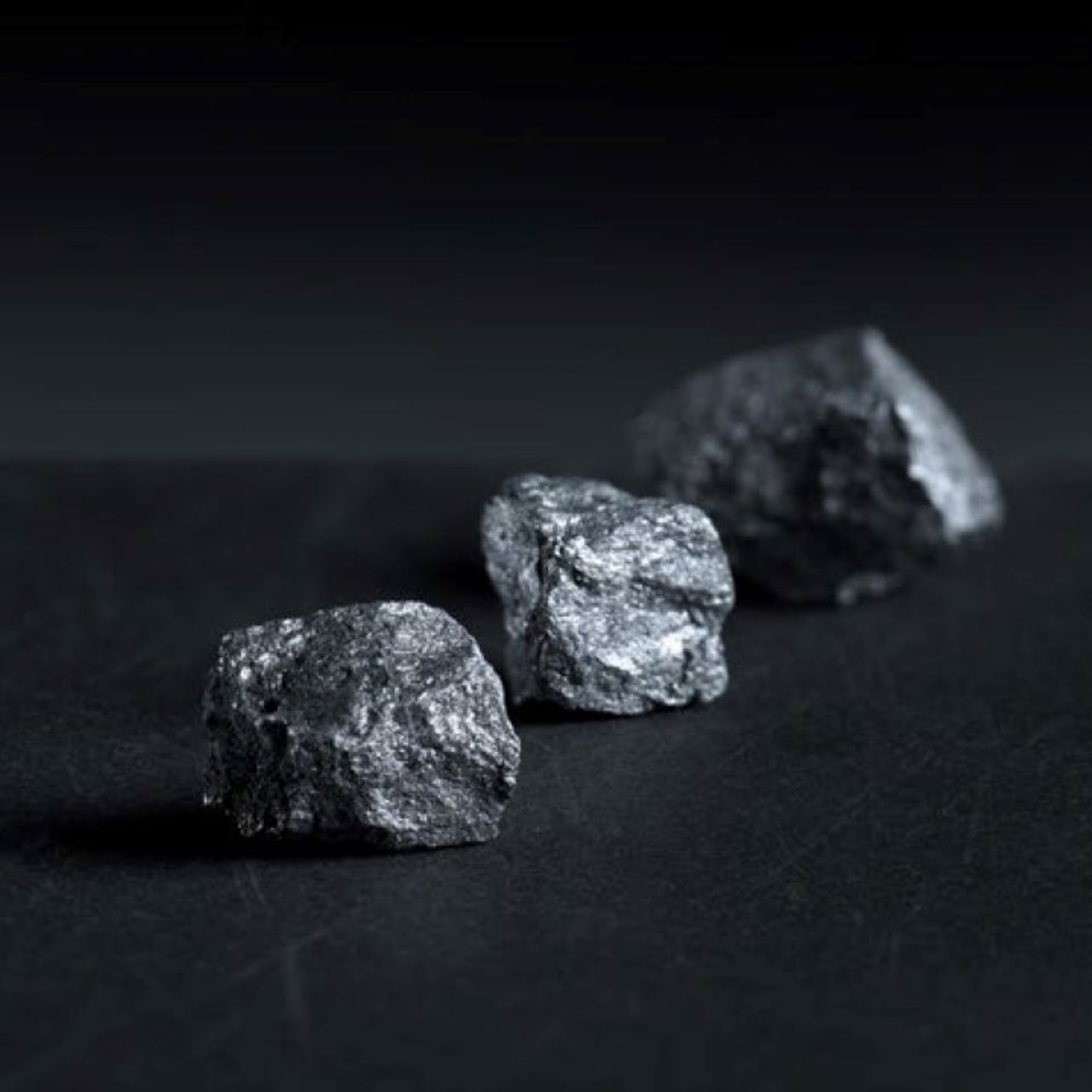
From quartz to silicon to silicones
What are the key properties of silicone rubber?
The performance of silicones is based on their unique chemical structure where silicon and oxygen (Si-O) molecules create high bond energy links. Silicone rubbers or elastomers leverage this base when compounded with reactive, straight chained molecules and a cross-linking agent. Radical, condensation or addition crosslinking reactions are used to meet precise processing and performance requirements such as the desired mechanical properties of the rubber silicone (elasticity, absorption, tear strength, etc.).
These elastomers can also be reinforced with mineral fillers, such as silica, alumina, calcium carbonate, silicone resins, etc. A wide variety of additives can also be integrated into the elastomer in its final composition for other specific characteristics (color, rheology, pot life, etc.) or performance standards (electrical insulation or conduction, heat transfer, fire retardancy, chemical adhesion, mold release, etc.).
Here are some of the main features of silicone rubber. In the next section we compare some of these characteristics with other types of rubber:
- Long-term durability and reliability in all environments
- Resistance and stability over a wide range of temperatures (from -50°C to 250°C) or to extreme outdoor exposure, including humidity, direct sunlight, water, ozone, etc.
- Flexible at low temperatures due to their low glass transition temperature (Tg)
- Readily resistant to electromagnetic and particle radiation (UV, alpha, beta and gamma rays)
- High thermo-oxidative resistance (-Si-O-Si- binding energy is higher than C-C bonds)
- High fire resistance
- Basic fire resistance is obtained thanks to PDMS backbone and inert fillers, but fire resistance can be enhanced with selected additives
- Non-toxicity of the smoke when burnt /Halogen-free
- Versatile elastomeric properties, including very high elongation before breaking point and/or strong resistance to tearing (essential in molds, modeling and reproduction, kitchenware, etc.)
- High-performance dielectric properties and thermal resistance to insulate and protect electrical and electronic equipment, including high voltage lines
- High water repellency and waterproofing, for use in a wide range of applications, from construction to industry, such as the making of watertight seals and gaskets in engines
- Biocompatibility, ideal for medical applications (skin contact, medical devices, long term implants, etc.), unconducive to microbiological growth, and their resistance to high temperatures enable them to be easily sterilized
- Excellent non-stick and non-adhesive properties for a wide variety of applications from molding release in industrial processes to cookware, where its low toxicity is also appreciated
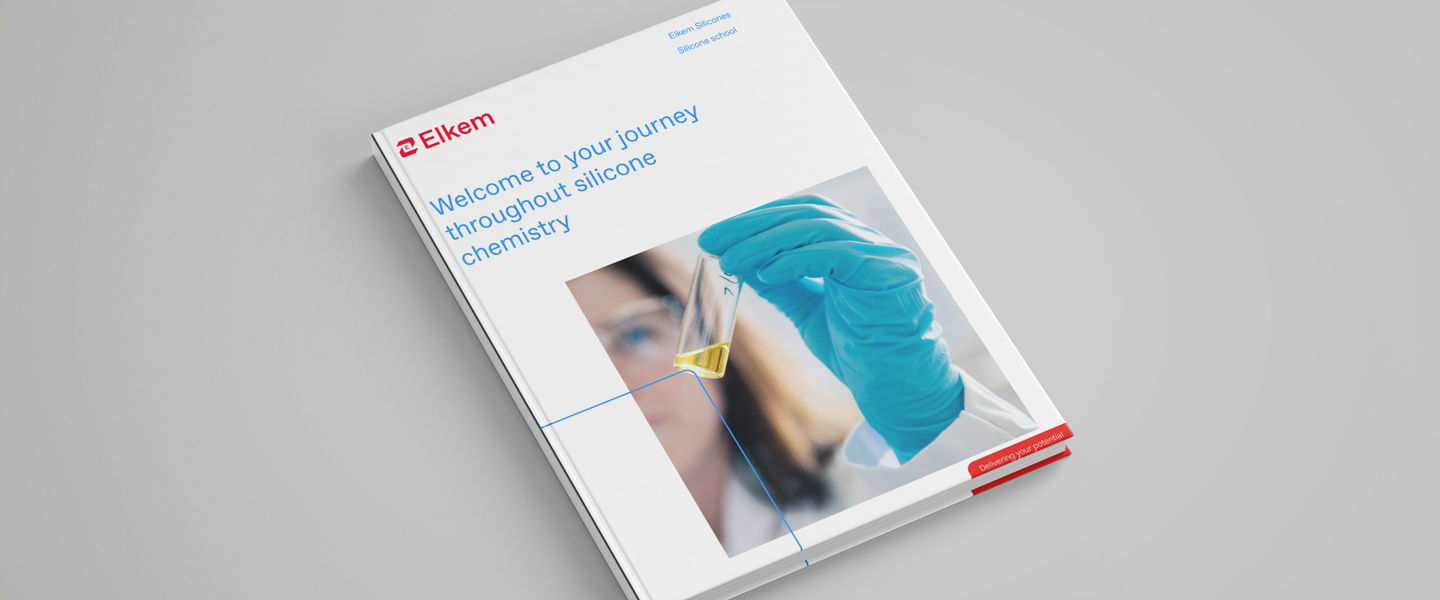
Guide du Silicone
Tout ce que vous devez savoir sur les technologies silicone.
What are the main alternative solutions to silicone rubber?
As we have summarized above, silicone rubber is used in high-performance applications, such as harsh environments, specialist medical or food applications or in demanding industrial processes. Silicone rubber is the best solution in most critical conditions, where other rubber or polymeric materials will fail.
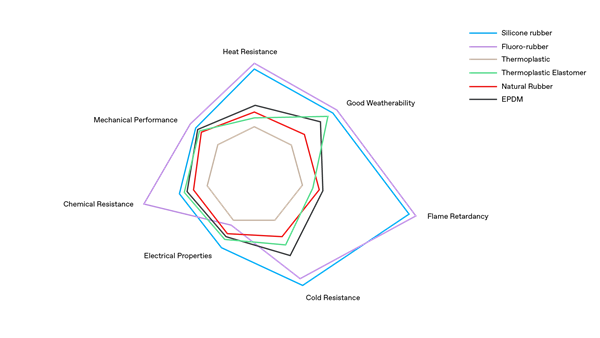
Silicone rubber: the customizable high-performance material for endless applications
While this blog has mainly focused on the technical attributes of rubber silicone, its underlying chemistry and how it compares to other materials, it’s important to end this overview by reminding our readers that rubber silicone is everywhere in their lives, whether they see it or not.
For example, at a time when energy issues are at the top of the world’s priorities, silicone rubber is essential in building innovative devices that harness renewables, such as windmills and sea turbines that could not function without the specific attributes of this versatile material. At the other end of the energy cycle, our home insulation, such as the sealants in our windows and doors, would not be nearly as efficient without silicone caulking.
Silicone molds, non-stick cooking utensils are also present in in our homes to make cooking easier and more enjoyable. Our ovens, refrigerators, dishwashers and other appliances of all sizes depend on silicone to provide us with efficient and reliable devices. From footwear to textiles, from smartphones to personal care and medical products, silicone allows us to be more comfortable, healthier and create more durable products.
Also, high on the quest for lower carbon emissions and cleaner energy, silicone rubber in various forms is an integral part of electrical and hybrid vehicle manufacturing, particularly in the insulation of engines and battery-pack management and the insulation of cables (for batteries, charging stations, etc.).