- Magazine
- Elkem around the world
- Elkem around the world: Nagpur, India
Elkem around the world: Nagpur, India
Dushyant Pathak joined Elkem without prior experience in foundry, a year after Elkem’s acquisition of the Nagpur plant in 2016. At the time, Dushyant had spent most of his 22-year long career working in precision engineering. When Dushyant started in his new role as a plant manager, he was determined to continue the work of converting the former culture towards the Elkem global standard, with a higher level of transparency, focus on safety, an innovative mindset, and an established value system. The plant had been in operation since with 1984 with low levels of automation and technological upgrades. This emphasized the need to focus on the safety of employees and contractors working at the facility, but it was also a unique opportunity to increase productivity and innovation with implementation of the Elkem Business System (EBS) methods.
With extensive experience from the automotive industry and the Toyota Production System working practices, Dushyant took on the challenge of implementing the EBS mindset at the Nagpur plant after the acquisition. "Everyone stayed and no one was replaced in the integration process" Dushyant says. Elkem introduced the plant and the employees to a new business system and the values it was built upon. Respect and involvement are two of the core values Dushyant emphasizes. "As a leader, I need to trust that the team is doing what they can do, and my responsibility is to provide the support and resources they need", Dushyant highlights and acknowledges that it is this kind of trust that empowers people. Moreover, Dushyant underlines the importance of active involvement of the employees. The plant utilizes an employee suggestion program to foster continuous improvement and active involvement of the employees. Last year, the plant's employees submitted around 900 suggestions. Many of these suggestions are implemented, and in total around 400 kaizens (improvements) were generated through the program.
Safety has also become an important aspect of the plant's operations. Every year, the team celebrates Road Safety week at the plant to show that safety is not about Elkem - it is about the people and their families. "Safety is our license to operate" Dushyant says and adds that they are working to improve the facility to achieve the goal of zero harm. The plant has seen a considerable reduction in injury rate after encouraging the employees’ active involvement in the Behaviour Based Safety (BBS) program. "All employees actively participate in identifying key behaviours and continuously observe and give feedback to coworkers to follow the same safe practices" Dushyant explains pointing out that their focus is on positive reinforcement.
As a result of the effort that Dushyant and the team have invested in improvements over the past years, the plant has seen higher levels of profit, customer acquisition, product development, and exports. Without radical changes in the plant's level of automation, the same plant and the same team doubled productivity by adopting a different culture and embracing new practices. "We have a long way to go, but I am very proud of what we have achieved so far" Dushyant states.
The Nagpur plant uses raw materials such as silicon, ferrosilicon, and scrap which are melted in induction furnaces and processed through a ladle alloying process with different alloying materials such as magnesium, calcium, rare-earth and barium to produce high-quality ferroalloys such as ferrosilicon magnesium, inoculants, high-quality inserts and master alloys . "Our state-of-the-art crushing and sizing facilities enable us to deliver the required sizes to our foundry customers" Dushyant says. Nagpur's foundry customers serve various industries with applications within automotive, engineering, energy, and utility, among others. The plant’s customers are mostly local and close to the plant, but around 12% of the plant's production is exported to different parts of the world.
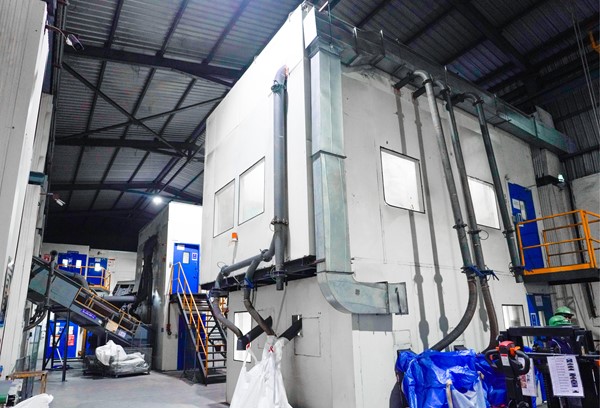
Elkem’s Nagpur plant is actively contributing to the local community by supporting education, health, and environmental initiatives. The plant's flagship program is called Wings Fly High, which is a collaboration with Sahyadri Foundation. "Wings Fly High is a bus converted to a computer lab that provides computer education to municipal school children who have no other opportunity to get computer access" Dushyant describes. Moreover, the program is mobilizing the community to enhance awareness and bring children who dropped out back to school. So far, this program has put more than 400 students through computer education and 150 students back to school. The program allows the students to practice on real computers in addition to theoretical studies, which have had a significant impact on the children.
There are many health facilities in the Nagpur area that needed upgrades. Last year, the plant helped 15 health centres with necessary upgrades. "We have improved the health infrastructure at nearby primary health centres with building out outpatient department (OPD) rooms, patient waiting areas, and provided more than 20 toilets to improve hygiene at local hospitals" Dushyant says. Additionally, the plant has provided healthcare equipment to government clinics to enable good health service to the community.
Dushyant and the team also work to ensure that the plant is a sustainable and responsible actor in the local community. In 2022, the plant installed 1,054 solar panels at the rooftop of the plant's facilities. This now generates 8% of energy demand. Another one of the plant's successful initiatives serves to promote circularity in their operations. This involves the reuse and recycle of wood pallets. The Nagpur team came up with the concept of reusing inbound pallets whenever possible and fix those that needed repair to avoid buying new ones, as part of the employee suggestion program. After a successful pilot shipment to China in June 2018 with repaired pallets, a larger project was launched. Pallet repair is now done using an internal setup. Following this initial success, all warehouses began reusing inbound pallets, resulting in additional waste reduction. Recently, a new initiative was also launched. To significantly reduce plastic load, used bags are sent to bag manufactures and recycled. The granules are added and makes up 20% of the plastics used in new bags.
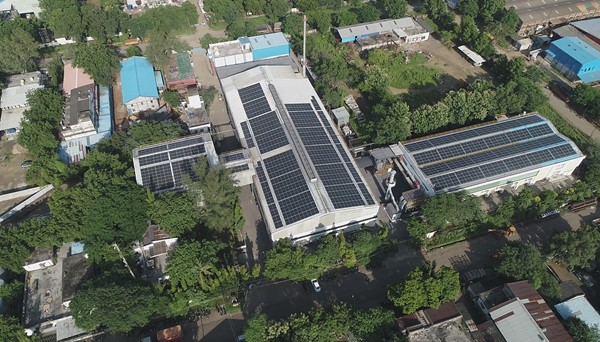
Recently, Elkem upgraded the plant with dust collectors and established an Internet of Things / Automation lab. Around 170 people currently work at the Nagpur plant, of which 85 are employees and the remaining are contractors. Every day, the team takes 5 minutes to do yoga together. "Creating a good place to work is important to retain talent" Dushyant explains. One of the initiatives aimed at creating a strong team culture is the “Fun Champions”. They participate in events together and try to do social activities outside of work. "This weekend we are running a 5k in a local race" Dushyant adds.
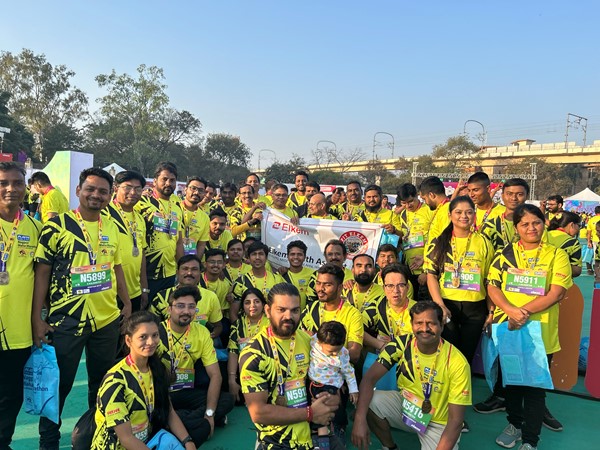
The plant is situated in MIDC Hingna, an industrial zone in the state of Maharashtra, India. Nagpur is a large city precisely at the centre of the country providing the plant with a unique position and great accessibility to its customers. "Staying close to our customers is very important to us" Dushyant emphasizes, while adding that they often invite the customers to the plant to facilitate better communication and collaboration. The plant has an R&D centre that does a lot of testing for the customers, and the team continuously work to develop new products for its customers. As a result of the customer-centric mindset, customer complaints have been significantly reduced. One of the issues that were crucial to address was the supplier quality. "The plant is in need of high-quality raw material in line with the Elkem standard, and we buy from various supplier sources” Dushyant mentions. This made the sourcing of raw material challenging for the plant. Hence, the plant created a dedicated Supplier Quality Agreement team that works with the suppliers to train, audit, and follow up, ensuring that they comply with the Elkem standards. Thus, the supplier rejections have been lowered from 45% to 8%.
When discussing long-term goals, the first thing Dushyant brings up is their plans to significantly increase production in Ferrosilicon magnesium (FSM) and Inoculants. Dushyant highlights that this will require more automation and new technology, but also competence. "I am very much looking forward to continuing the development of the team," Dushyant adds while highlighting the importance of developing talent and expertise internally. Lastly, Dushyant underlines the aim of becoming a true lean organization with more scientific problem-solving, lean practices to utilize the flow, stability tools across the value chain, and a true EBS culture.
You can read more about the plant on Nagpur's local page