- Magazine
- Elkem around the world
- Elkem around the world: Joinville, Brazil
Elkem around the world: Joinville, Brazil
Elkem’s Joinville plant, under the leadership of plant manager Samuel Beghine, has won awards for both its commitment to safety and its Elkem Business System (EBS) practices. The plant has also taken steps to address environmental challenges by installing solar panels, implementing an industrial water reuse project, and collecting rainwater for use in the production process. In this article, Beghine shares the story of how the Joinville team has shaped the plant’s successful operations from the beginning.
Samuel Beghine started working in Rhodia Silicones as a chemical process operator at the age of 20 while studying to become a chemistry technician. "I fell in love with working with silicones," he shares. About 5 years later, Rhodia Silicones was acquired by Bluestar (renamed Bluestar Silicones International) which also acquired Elkem in 2011. Following these changes, it was decided that the silicones production lines from Rhodia's plant in the city of Santo André would be transferred to Joinville. "I came to Joinville as a production supervisor working with the former plant manager, Clarisse Rodriguez, to help build the plant," Beghine explains while adding that this change meant a lot to his career. Together with the rest of the team, they worked hard to achieve the results in Joinville we are looking at today. The move also gave Beghine the opportunity to gain experience in various positions at the plant until he replaced Rodriguez in 2023 and landed his current role as the plant manager.
Moving the silicones production lines to Joinville made sense due to its proximity to ports. The plant is well located within an industrial park with a good structure. “Joinville is a prosperous and safe city with a great quality of life” the plant manager describes. Within a radius of 100 km there is a lot of nature to enjoy. However, due to the limited number of chemical companies in the region, the big challenge has been to find qualified labour and retain people. As a countermeasure, Elkem has partnered with a local organization to bring a chemical process operator course to the city, which has been a successful program.
EBS and Safety
For the past two years, the plant has won the Elkem Business System (EBS) award and the Elkem environment, health, and safety (EHS) award. When asked about the key to the team’s success, Beghine says “We work with the team on a daily basis, involving everyone by showing them the importance of working with the EBS methodology and commitment to safety.” About the EBS culture, he states that while they do give awards at the end of the year to people who have done outstanding work, it needs to be supported and encouraged on a daily basis. Safety is also high on the team’s agenda. The safety award was a result of the plant’s long-term efforts. “We have worked systematically to develop robust safety policies and procedures, promote a safety culture in the organization, and set clear, specific and measurable targets to prevent accidents in the workplace” Beghine says. Joinville’s path towards safety excellence has included carrying out various activities such as accident prevention, training, regular audits of safety practices, use of innovative technology, and more. “Achieving a safety award after many years of hard work requires a daily commitment to the safety and well-being of employees at work” the plant manager underlines.
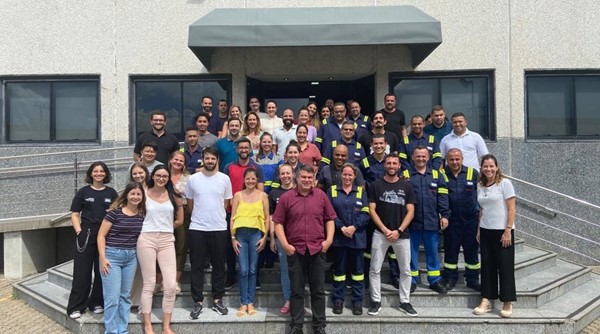
The production
The Joinville plant produces silicone oils, anti-foaming agents and compounds. “Our main raw material is silicone monomer which undergoes a polymerization process” Beghine says. Polymerization is a process where the plant produces raw materials for other production lines. “We produce oils for the cosmetics line, anti-foam for the agricultural market, and silicone rubber for the automobile market” Beghine highlights.
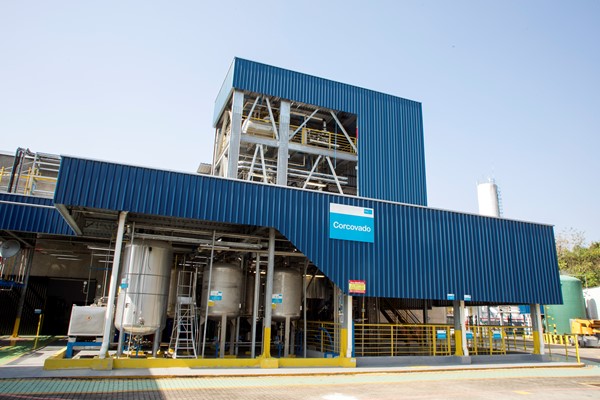
Installation of solar panels for electricity generation
One of the environmental challenges facing the industrial sector is the search for renewable energy sources that reduce the environmental impact of the production processes. In 2023, Joinville has installed solar panels on the roof of the plant to generate solar energy. The solar panels increase the energy efficiency of the production unit in Joinville and generate 40% of the electricity consumption on the site. “By including this form of energy generation, Joinville has reduced its CO₂ emissions by 48.12 tons - which is equivalent to saving 295 trees,” the plant manager says. The project made it possible to diversify the plant's energy matrix in line with Elkem's global sustainability goals.
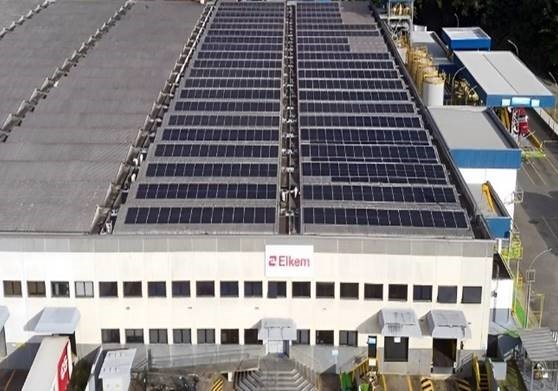
Employee initiative recovers 500,000 liters of water
The industrial water reuse project initiated in 2019, originated from a study carried out by a group of employees who saw an opportunity for improvement. “The project resulted in a 65% reduction in water waste volume” Beghine confirms. The plant uses a reverse osmosis process to demineralized water for steam generation used to heat the reactors to produce silicones, compounds, anti-foaming oils and emulsions. With an average flow rate of 700 liters per hour, the process previously generated 780,000 liters of waste per year, which was sent for external treatment and subsequent disposal. With the implementation of the new treatment unit, an average of 500,000 liters of water per year are being recovered. The remaining 280,000 liters are now used in the gas scrubber which neutralizes harmful components in the atmosphere. Eventually, this water is collected for external treatment to prevent environmental damage.
Rainwater collection for use in the production process
In addition to the wastewater recovery project, Joinville has a system for using rainwater in the production process. Rainwater is collected, filtered, and stored in a reservoir. From the reservoir, it goes to the cooling tower and is then used in the production process. Both “water-initiatives” contribute to the development of a circular economy and business model, providing less environmental impact and reducing annual water and effluent treatment costs.
In the future, Beghine conveys that he wants to see the plant grow and expand. “We will continue working on optimizing our processes to remain competitive, and we aim to be a benchmark within Elkem in terms of safety, quality and EBS” Beghine concludes.