- Magazine
- Elkem around the world
- Elkem around the world: Chicoutimi, Canada
Elkem around the world: Chicoutimi, Canada
Meet Charles Tremblay – Chicoutimi’s plant manager during the day and a hockey coach at night.
Charles Tremblay joined Elkem in 2011 as a technical manager without prior experience in the silicon-based materials industry. “As a technical manager your role is to lead projects, manage contracts, and maintain the equipment”, Tremblay mentions. However, his responsibilities changed considerably after becoming Chicoutimi’s plant manager in 2015. "As a plant manager, my job became managing people: ensuring everyone shares the same vision and moves in the same direction”, Tremblay states.
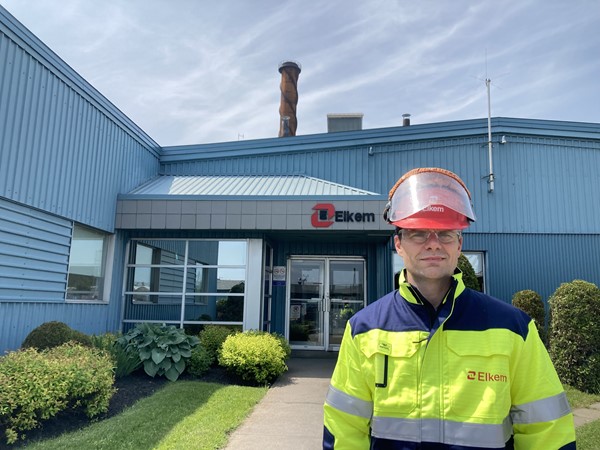
Leadership with intent
“In this role, you must wholeheartedly and constantly embrace the myriad of challenges that come your way”, Tremblay says with a smile. Despite giving a considerable amount of thought to the plant even outside its premises, he also makes sure to prioritise time with his family in the evenings.
During the winter, he coaches his son’s hockey team after work. Interestingly, he can draw a few parallels between his work at the plant and his role in the rink. “Coaching is not telling someone what to do, it is helping them understand the problem and find their own solutions to it”, Tremblay says. Furthermore, Tremblay emphasizes the significant influence being passionate about one’s work have in both areas. “Hockey is a high-intensity sport and coaching the kids on the ice is the real benchmark test”, he admits. You coach the players for 60-90 minutes at the time, which is only a fraction of the time you have to instil the same passion with the team at the plant”, Tremblay conveys.
Effective leadership is of great importance to the plant manager, as he acknowledges its role in driving change and fostering growth within teams. “To me, it is crucial that people feel both seen and heard”, he responds when asked about his approach to being a leader. “As a leader you need to be a good listener and ensure that you provide the team with the resources and support that they need”, Tremblay underlines.
The plant
One of the unique benefits to the plant’s location is its access to the hydropower plant connected to the Chicoutimi River. The power plant is closely tied to the plant’s history starting in 1967. Today, the plant is the workplace for around 100 Elkem employees. It mainly produces foundry alloys and ferrosilicon made from quartz, iron, wood chips, and coal. Elements, such as magnesium, are added through the alloying station. Subsequently, metal is refined to produce value-added products that fall under the two main categories: Ferrosilicon Magnesium (FSM) and Inoculants.
Chicoutimi’s customers are predominantly foundries. Both FSM and Inoculants are used to improve the quality of castings in different ways. FSM transforms grey iron into ductile iron and Inoculants is a family of products used to improve the casting in the inoculation process. “Overall, we can produce around 100 different products on this site”, Tremblay shares. To manage this complexity, their production of FSM and Inoculants run in alternating cycles requiring the plant and the employees to be agile and flexible.
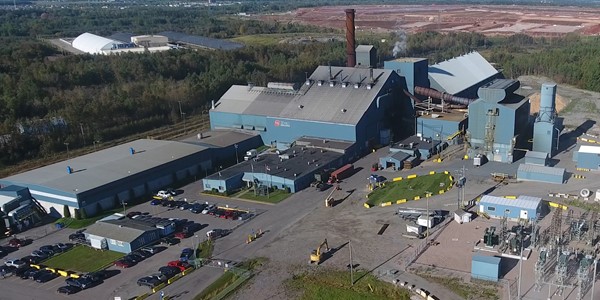
Safety
For many, 2021 was a year overshadowed by a global pandemic, but to Tremblay it became a wake-up call. “I had to take a hard look in the mirror and re-evaluate the direction we were headed”, he admits. After several incidents and high potential near misses, it was clear that something had to change.
One of the challenges the plant has been facing over the past years is the demographic shift in its workforce. A significant influx of new operators lead to heightened pressure on the plant’s more seasoned leaders and supervisors to ensure safe operations. The solution was an increased focus on leadership development. “We created what we call the Enhanced Safety program where we bring enhanced risk awareness to the employees”, Tremblay explains. The program contains internal tools, such as the Safety Passport, which is an analysis tool used before starting a new task. Tremblay acknowledges the substantial progress they have made in this area, but also recognizes that there is still work to be done.
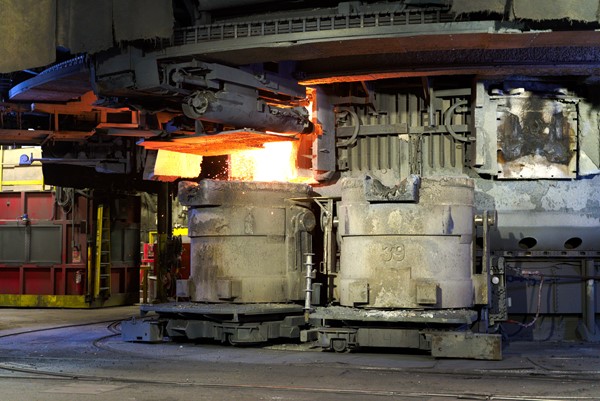
Customer centricity
One of the site’s main advantages is the proximity to their customers. Customer centricity is at the core of their operations and well-integrated in the team’s mindset. “Personally, I like to work with our Sales team and sometimes visit the customers to discuss their needs and address any challenges they have”, Tremblay notes. Staying close to the customer is also important in terms of identifying new opportunities and understanding the evolving needs of the industry. “It provides us valuable insights that enable us to innovate and tailor our offerings”, he adds. Furthermore, all units at the plant are educated to understand their customers’ needs and concerns. “Our main task is to deliver stability to our customers, and to achieve this we all need to understand why this is critical”, Tremblay emphasizes. Moreover, the plant manager underlines the important role the EBS philosophy plays in order to achieve quality and stability in their production.
Local community
The plant is supporting several philanthropic groups that promote meaningful causes. One of the initiatives are aimed at local schools in the area. The contributions cover scholarships to young talents as well as need-based funding to students that are struggling to make ends meet.
Additionally, the Chicoutimi plant supports another non-profit that has made great impact on them. It is a local organisation that works with kids suffering from cancer and their families. In addition to providing funding, the Chicoutimi team also participates in fundraising activities to support the cause. “It means a lot to see how close the people working at the organisation are to the kids and to know that we are able to make a difference for them”, Tremblay affirms.
From crazy ideas to execution
The Chicoutimi team values an open culture and an innovative mindset. “Sometimes it leads to crazy ideas, but we try to look at the possibilities rather than the constraints”, Tremblay articulates. A notable example is the approach they adopted for replacing an existing furnace.
During a capacity increase project in 2014, a team member proposed the unconventional idea of relocating the furnace outside the plant instead of blasting the furnace from the inside of the plant. While the new method had never been tested before, instead of dismissing the suggestion, the team got to work. Using specialized equipment, they were able to transport the old 800 mt furnace out of the plant and bring in the new furnace. The novel idea proved to be much safer, and the achievement stands out as a testament to the team’s commitment to embracing innovation.
Excited about the future
Last year was a highly successful year for the team. “If you look at the numbers you see great success, and if you look beyond the numbers, you see a lot of people who worked very hard” Tremblay highlights. “I am extremely proud of the team and what we have accomplished so far”, Tremblay expresses. When asked about the road ahead, Tremblay adds “we need to adapt to the changing landscape of our industry, but I am more than confident in our ability to handle the future”.